3. Die Fortschritte des 19. Jahrhunderts
Der Saigerprozess war nicht billig. Er hat sich lange gehalten und es bedurfte der Fortschritte der Chemie der 1. Hälfte des 19. Jahrhunderts, bis man eine Alternative zu dieser Arbeitsweise gefunden hatte. Diese Neuerung war die Amalgation. Es kam also Quecksilber ins Spiel. Auf der Gottesbelohnungshütte wurde von 1825 bis 1827 das Amalgamierwerk gebaut. Das Gebäude ist – nebenbei gesagt – historisch und bis heute erhalten. Nach seinem Architekten wird es allgemein der „Schinkelbau“ genannt (Bild 6).
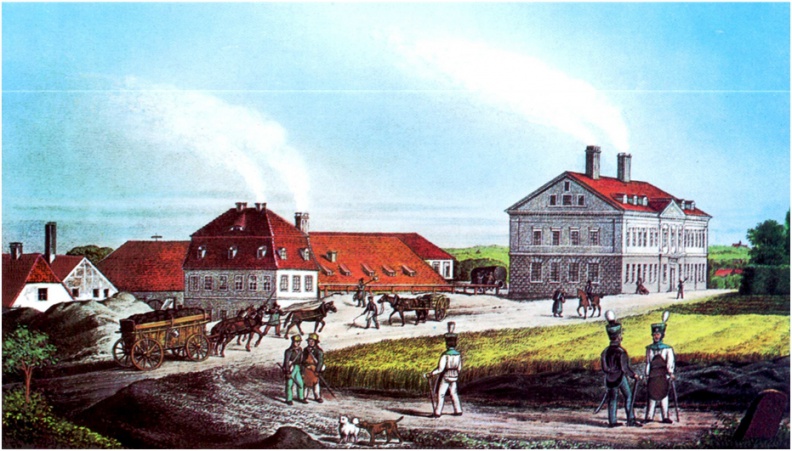
(Zeichnung Giebelhausen, Archiv Mansfeld Museum, Hettstedt)
Zur Amalgation war eine Vorstufe nötig. Vormaterial war natürlich weiter der Kupferstein, in dem das Silber als Sulfid vorliegt. Dieses muss zunächst in ein lösliches Silbersalz umgewandelt werden und zwar in Silberchlorid (Bild 7).
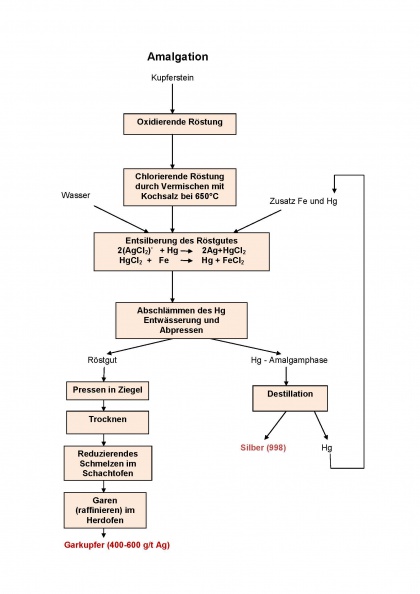
Hierzu wurde der Kupferstein zunächst einer oxidierenden - sulfatisierenden - Röstung und anschließend einer weiteren (chlorierenden) Röstung unterworfen. Dabei wurde das Röstgut mit Kochsalz vermischt und mit Wasser breiig angerührt und somit in diesem zweiten Schritt chlorierend geröstet. Bei 650 °C zerfallen die Sulfide des Eisens und des Kupfers in ihre Oxide. Dabei entsteht SO3. Dieses setzt aus dem Kochsalz Chlorid frei, welches das Silber in Silberchlorid umwandelt.
Das Röstgut wurde anschließend mit Quecksilber vermischt und metallisches Eisen zugesetzt. Es läuft dann folgende Reaktion ab: s.Bild 7
2 (AgCl2)- + Hg ==> 2 Ag + HgCl2
HgCl2 + Fe ==> Hg + FeCl2
Das Quecksilber stand damit zur Fortsetzung der Reaktion zur Verfügung, während das Silber vom Quecksilber gelöst (amalgamiert) wurde. Das entsilberte Röstgut wurde von Quecksilber abgeschlämmt, auf Nutschen entwässert und mit Ton und Kalk zu Ziegeln geformt und getrocknet. Die Ziegel wurden im Schachtofen auf ein Kupfer mit ca. 90% Cu verschmolzen, das in Herden gegart – raffiniert – wurde. Das so gewonnene Garkupfer enthielt noch 400 bis 600 g/t Silber – also mehr als das Saigerkupfer, weshalb auch weiterhin gesaigert werden musste. Auch reichte die Kapazität des Amalgamierwerkes nicht aus.
Das Quecksilber enthielt 0,7 % Silber und das Silberamalgam ließ sich abpressen. Das Silberamalgam wurde destilliert und es blieb ein relativ reines Silber (998 Feine) zurück.
Schon wegen der relativ hohen Silbergehalte im Garkupfer war man auch mit dem Amalgationsverfahren nicht so recht glücklich. Auch die belastende Arbeit mit Quecksilber war ein Nachteil. Also musste weiter nach Alternativen gesucht werden, die schließlich der damalige Leiter des Amalgamierwerkes, Augustin, fand.
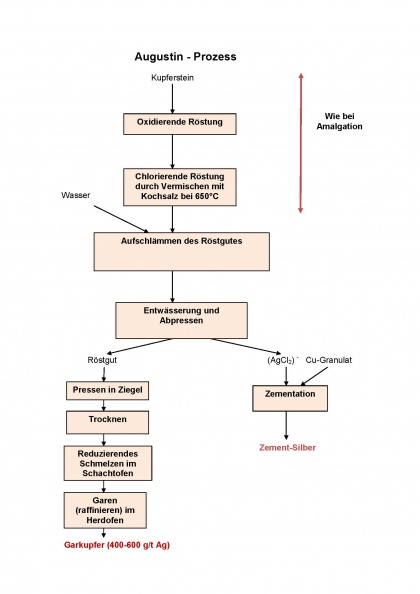
Er umging den Zementationsvorgang mit Quecksilber. Es blieb aber wie beim Amalgamierverfahren bei der chlorierenden Röstung. Nach einer Aufschlämmung des Röstgutes wurde die Silberchloridlösung abfiltriert. Das Silber wurde nun mit Kupfergranalien auszementiert. Durch Gegenstromführung von Lauge und Kupfergranulat gelang es einerseits, ein kupferfreies Zementsilber und andererseits eine entsilberte Lauge zu erzeugen, die nach der Auszementation des Kupfers mit Eisen abgeschlagen werden konnte. Die entsilberten Laugerückstände (aus dem Röstgut) wurden wie bei der Amalgation weiter verarbeitet.
Der Augustinprozess ermöglichte Ende 1843 zwar die Einstellung der Saigerung, beseitigte aber den Nachteil des Amalgationsverfahrens – die Silberverluste – nicht, auch wenn diese vergleichsweise zum Amalgationsverfahren etwas geringer waren. Und wieder inspirierte das zunehmende Wissen in der Chemie und über das Rösten zu einer Neuentwicklung – dem Ziervogelprozess.
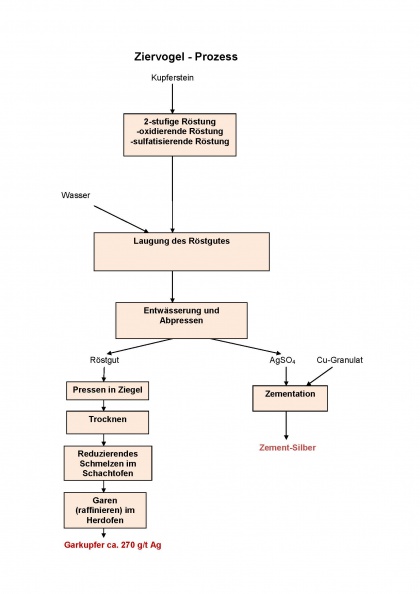
Die Entwicklung dieses Verfahrens wurde von der Tatsache befördert, dass sich in der ersten Röststufe bei der Amalgation (sulfatisierende Röstung) neben Kupfer- und Eisensulfat zum Teil auch Silbersulfat bildete. Dieses ist in heißem Wasser - wenn auch nicht besonders gut - löslich.
Man musste also in der Röstung erreichen, dass die Sulfatisierung des Silbers vollständig erfolgte. Das gelang, indem man die erste Röstung heißer führte, wobei sich die Sulfate zum größten Teil wieder in Oxide zersetzen. In einer zweiten Stufe wurde die Temperatur auf 900 bis 950°C erhöht. Jetzt zersetzten sich auch die restlichen Sulfate. Das frei werdende SO3 überführte das in der ersten Röstung entstandene metallische Silber sowie restliches Silbersulfid in Silbersulfat (AgSO4).
Das hört sich alles einfach an, war es in Wirklichkeit aber nicht. Die Anforderungen an die exakte Temperaturführung waren hoch, die damaligen Messgeräte gelangten an ihre Grenzen. Auch störten Nebenbestandteile die Bildung des Silbersulfates, sodass die gelungene Röstung letztlich für den Erfolg des Ziervogelprozesses entscheidend war.
Das Röstgut wurde anschließend schwach schwefelsauer gelaugt. Die Weiterverarbeitung der Produkte erfolgte wie beim Augustinprozess. Das Silber hatte nach dem Einschmelzen eine Feine von 999 bis 999,5. Aber auch an der Verarbeitung der Laugerückstände musste im Interesse des Silberausbringens noch gearbeitet werden (Nachrösten, Laugen). Das damals so erzeugte Kupfer enthielt immer noch 270 g/t Silber.
Die oben genannte Entwicklung wurde natürlich von der Entwicklung der Erzverarbeitung in den Rohhütten (z. B. Kupferkammer, Eckhardhütte, Kreuzhütte, Mittelhütte) befeuert. Der Bergbau konnte zunehmend mehr Erz liefern. Die Leistung der Rohhütten stieg von 12.000 t Erzdurchsatz im Jahre 1820 auf 28.000 t im Jahre 1850, um dann mit einer erheblichen Steigerung innerhalb von 20 Jahren, also 1870, mit 155.000 t aufzuwarten.
Ermöglicht wurde die Leistungssteigerung der Rohhütten vor allen Dingen durch den Ersatz der Holzkohle durch Koks. Doch diese Umstellung war mehr als Holzkohle raus und Koks rein! Die Schachtofenkonstruktionen mussten verändert werden und zwar durch Verengung der Ofenschächte. Blasebälge konnten weder die nötige Windmenge und -geschwindigkeit aufbringen noch den Druckwiderstand der deutlich höheren Beschickungssäule überwinden. Inzwischen gab es aber leistungsfähige Gebläse.
Die Veränderungen an den Öfen erforderte ein langwieriges Experimentieren. Es dauerte fast 100 Jahre (!), ehe eine brauchbare Relation von Querschnitt in der Düsenebene, der Form des Schachtes und der Höhe der Beschickungssäule gefunden wurde. Innovation war also nicht nur bei der Entsilberung sondern auch auf den Rohhütten gefragt.
Und noch eines sei hier erwähnt: Man erkannte auch, dass auch die Rohhüttenschlacke als Wertprodukt genutzt werden konnte und stellte Blähschlacke - zunächst in glasiger Form - her. Aber erst, als man kristalline Schlacke durch langsame Abkühlung - Tempern - herstellen konnte, eignete sich die Blähschlacke hinreichend für Bauzwecke. Schließlich gelang es auch Pflastersteine herzustellen, die noch heute in ganz Mitteleuropa zu finden sind (Bild 10).
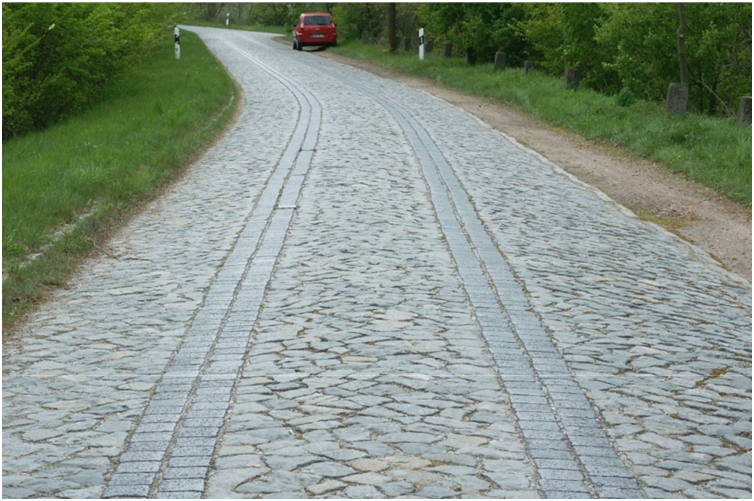