Im Jahre 1907 gegründeter Verarbeitungsbetrieb für Kupfer- und Kupferlegierungen. Noch heute als Mansfelder Kupfer und Messing GmbH (MKM) größtes Industrieunternehmen der Region.
Objektbeschreibung
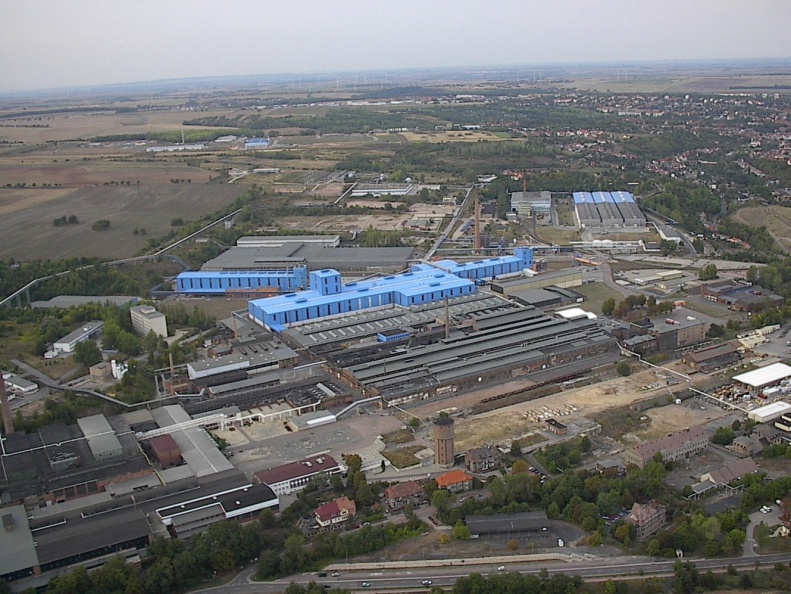
Im Jahre 1907 gab es einen Beschluss der Mansfeldschen Kupferschiefer bauenden Gewerkschaft, ein Werk zur Erzeugung von Halbzeugen aus Kupfer und Messing aufzubauen, da die vorhandenen Kapazitäten in Rothenburg und Eberswalde die Nachfrage nicht mehr decken konnten.
Das Werk nahm 1909 auf dem Areal zwischen Hettstedt und Großörner seine Tätigkeit auf. Es wurden Drähte, Bleche, Bänder, Stangen, Rohre und Profile erzeugt. Ab Mitte der 1920er Jahre erfolgte die Veredlung von Kupferdrähten (isolierte Drähte).
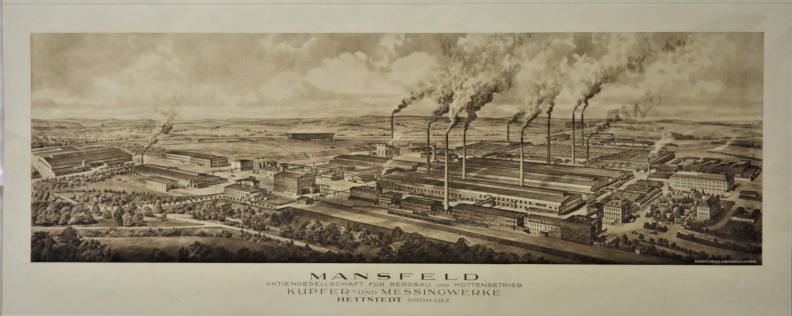
1934 nunmehr im Verbund der Mansfeld AG folgten Halbzeuge aus Aluminium und dessen Legierungen zum Absatz an mitteldeutsche Flugzeugwerke, z.B. für Junkers in Dessau.
Nach dem 2. Weltkrieg erfolgte keine Demontage, sondern Weiterführung als Sowjetisch-Deutsche-Aktiengesellschaft, ab 1.1.1954 als Volkseigener Betrieb (VEB). In dieser Zeit produzierte man auch Stahlgrobbleche, Stahlkaltband und Stahlprofile. Das war bis Mitte der 1980er Jahre der Fall.
Im weiteren Verlauf kam es zu einem ersten großen Entwicklungsabschnitt mit dem
- Neubau einer Aluminiumgießerei, einer
- Erweiterung der Aluminium-Blech-Band-Fertigung, u.a. durch Neuanschaffung moderner Walzmaschinen, dem
- Neubau einer Kupferlackdrahtfabrik. Ebenso einer
- Modernisierung der Kupfer/Messing-Bandfertigung, ebenfalls durch Neuanschaffung moderner Walzgerüste. Auf energetischem Gebiet folgte die
- Ergänzung des Betriebswassersystems mit Wasser aus der Harzer Rappbodetalsperre.
Die Jahre ab 1970 brachten, nunmehr im Verbund des Mansfeld Kombinates, eine zweite große Entwicklungsetappe mit
- Modernisierung des Schwermetall (Kupfer/Messing) Rohr- und Stangenzuges, dem
- Neubau eines Kupferdraht-Grobzuges, dem Neubau des Schwermetall-Bandwalzwerkes II, dem
- Neubau eines Kupferdraht-Feinzuges, der
- Umstellung der Prozesswärmeerzeugung auf russisches Erdgas und dem
- Bau einer 110kV Umspannstation zur Sicherung einer störungsfreien Elektroenergieversorgung.
All diese Maßnahmen führten gleichzeitig zu einer wesentlichen Verminderung der Umweltbelastung des Territoriums.
Während der gesamten Zeit nach dem 2. Weltkrieg unternahm man große Anstrengungen zur Produktion von Konsumgütern wie Schnellkochtöpfen, Alpaka-Bestecken, Fahrradfelgen aus Aluminium-Legierungen u.a.m.
Nach der politischen Wende wurde das Werk in erheblichem Maße umstrukturiert. Einige Fertigungsbereiche und Sortimente verschwanden vollständig, Produktionshallen wurden abgerissen, Hilfs- und Nebenabteilungen ausgegliedert (privatisiert) und Sozialeinrichtungen in kommunale Verantwortung übergeben. Die Anzahl der Beschäftigten verminderte sich in diesen Zusammenhängen von früher max. 9000 auf 1000, Damit ist das Werk aber noch immer einer der größten Industriebetriebe des Landes Sachsen-Anhalt. Im April 2016 werden für das Unternehmen 1261 Beschäftigte angegeben.
Zahlen und Fakten
Das Areal des Betriebes umfasste 1990 ca. 1,5 km2, davon waren ca. 70% bebaute Fläche. Dieser Wert verminderte sich nach 1990 durch Ausgliederungen im Zusammenhang mit Privatisierungen.
Der Produktionsumfang betrug in den 1970/1980er Jahren (jeweils Spitzenwerte)
- Halbzeug aus Kupfer und dessen Legierungen 120 000 t
- Halbzeug aus Messing 20 000 t
- Halbzeug aus Bronze 2 000 t
- Halbzeug aus Neusilber 2 000 t
- Halbzeug aus Aluminium und dessen Legierungen 130 000 t
- Stahlgrobbleche 300 000 t
- kaltgewalzter Bandstahl 40 000 t
Dazu kamen noch viele kleinere Positionen, was sich aus der Legierungsvielfalt, d.h. aus den chemischen und physikalischen Parametern, den Angebotsformen usw., aber auch aus den aus Bilanzentscheidungen herrührenden Klein- und Kleinstmengen-Zuteilungen ergab.
Der Exportanteil war verhältnismäßig gering, er betrug weniger als 10% der Gesamtproduktion.
Die elektrische Anschlussleistung lag in der Spitze bei 45 MW.
Die Prozesswärmeversorgung erforderte zunächst den Einsatz von ca. 280 t/Tag Braunkohlenbriketts, woraus im werkseigenen Generator max. 700 000 m³ Gas entstanden. Nach Erdgaseinsatz im Jahre 1974 verminderte sich der Gasverbrauch mengenmäßig auf weniger als die Hälfte.
Das Werk hatte einen Geamtwasserbedarf von ca. 25 000 m³/Tag, wovon freilich ein bestimmter Anteil im Kreislauf gefahren werden konnte.
Der Materialumschlag betrug ca. 800 000 t/a, wovon 90% über die Schiene abgewickelt werden konnten.
Die Belegschaft umfasste in der Spitze bis zu 9000 Personen, davon dürften ca. 5000 mehr oder weniger direkt in der Produktion beschäftigt gewesen sein. Dazu kamen ca. 1500 Personen als Hilfspersonale in Werkstätten, der Energieversorgung und im Transport.
Agestellt waren ca. 2500 Personen, ing.-technisches Personal - Ausbildungs-, Betreuungs- und Sozialeinrichtungen einbegriffen.
Im Jahre 2005 hat MKM ca. 200.000 t Halbzeuge vorzugsweise aus Kupfer und nur zum geringen Teil aus dessen Legierungen mit nur noch ca. 1000 Belegschaftsmitgliedern produziert. Die Eigenerzeugung von Kupfer aus Sekundärrohstoffen ist eingestellt. Eine erst 1999 mit nennenswertem Investaufwand vorgenommene Erweiterung der entsprechenden Einrichtungen wurde mit der Gesamtanlage einschl. der Kupferelektrolyse Anfang 2003 stillgelegt, bzw. verkauft. Im Betriebsteil „Süd“ ist nur noch die 1967 von Krupp aufgebaute vertikale Stranggußanlage Mansfeld II in Betrieb.
Zeittafel
[027] | Zeitpunkt bzw. von | bis | Ereignis |
1818 | 1857 | Die Werke Rothenburg /Saale und Eberswalde im Verband der Mansfeldschen Kupferschieferbauenden Gewerkschaft sind die Vorläufer des Hettstedter Betriebes. | |
1909 | MKM (Mansfelder Kupfer und Messingwerk) nimmt die Produktion auf und erweitert damit die Kupferhalbzeugpalette der Mansfelder Gewerkschaft. Ferdinand Bleicher hatte die Planung geleitet. Otto Busse führte dann das produzierende Werk, das bereits im 1. Weltkrieg wichtiger Zulieferer für die Rüstungsindustrie wird. | ||
1921 | Die Mansfelder Gewerkschaft mutiert zur Mansfeld AG. | ||
1927 | Hermann Brucklacher übernimmt die Leitung des Werkes, die er bis 1945 innehat. | ||
1933 | Aus Subventionierungsgründen wird für die Bergbau- und Hüttenbetriebe die Mansfeld AG für Bergbau und Hüttenbetrieb gegründet. MKM wird zum zentralen Betrieb der Rumpf-Mansfeld AG. | ||
1934 | In Hettstedt beginnt die Produktion von Halbzeugen aus Aluminium und dessen Legierungen. | ||
1941 | 1945 | Hettstedt produziert wiederum für die Kriegsrüstung, diesmal auch mit Hilfe von zwangsverpflichteten ausländischen Arbeitskräften und Kriegsgefangenen. | |
1945 | Im April/Juni 1945 fällt das Werk unter US-amerikanische Besatzung. | ||
07. 1945 | Die sowjetische Besatzungsmacht übernimmt das Werk, das schrittweise in Gang gesetzt wird und bis Ende 1953 als Sowjetisch-Deutsche Aktiengesellschaft (SDAG) geführt wird. Als Generaldirektoren fungieren die sowjetischen Bürger Lirow und Karjakin. | ||
01.01.1954 | Das Werk wird Volkseigener Betrieb (VEB). Generaldirektor wird Prof. Dr. Franz Bandel. Es folgt eine stürmische Entwicklungsetappe. Hettstedt wird Leitbetrieb einer weiteren Gruppe von Nichteisenmetall-Halbzeug-Betrieben als VEB NE-Metallkombinat. | ||
1968 | Prof. Bandel geht in den Ruhestand, die VVB NE-Metallindustrie in Eisleben wird aufgelöst, ihr Generaldirektor Stude übernimmt das Hettstedter Werk. | ||
1968 | Zwecks Erweiterung der Al-Halbzeug-Produktion übernimmt Hettstedt den Aufbau des auf dem Gelände des auslaufenden Braunkohlenwerkes Nachterstedt zu errichtenden neuen Betriebes. | ||
01.01.1970 | Hettstedt wird mit allen zugehörigen Werken vom VEB Mansfeld Kombinat Wilhelm Pieck, Generaldirektor Prof. Dr. habil. Karlheinz Jentsch, übernommen. Die vorher zu Hettstedt gehörigen Werke unterstehen nun dem Kombinat direkt. Es folgt eine zweite bemerkenswerte Entwicklungsetappe. | ||
1972 | Das im Aufbau befindliche Werk Nachterstedt wird selbständig und dem Kombinat direkt unterstellt. | ||
1990 | Hettstedt wird Treuhandbetrieb, firmiert zunächst als Walzwerk Hettstedt AG und wird von westlichen Konkurrenzbetrieben zwecks evtl. Übernahme sehr intensiv kontaktiert. | ||
1992 | Der gesamte Aluminiumteil wird ausgegliedert (privatisiert.) | ||
1993 | Im Zuge der Auflösung der Mansfeld AG wird die Kupfer-Silberhütte MKM zugeordnet. MKM firmiert nun als Mansfelder Kupfer und Messingwerk GmbH und bleibt bis 1995 in Treuhandverantwortung mit schnell wechselnden Geschäftsführern ohne erkennbare Konzeption zur Weiterführung des Werkes. | ||
1995 | Die belgische Lamitref Industries N.V. privatisiert das Werk und und qualifiziert die schon früher eingeleitete Umstrukturierung und Sanierung u.a. durch eine großzügige Investitionspolitik. | ||
2004 | Die kasachische Kazakhmys Corporation übernimmt das Werk von Lamitref. | ||
2013 | Übernahme durch die Copper Bidco GmbH der Investorengruppe Hannam & Partners (London) | ||
Februar 2019 | Verkauf an die KME-Gruppe mit dem Stammsitz Osnabrück | ||
1. Juni 2019 | Die MKM Mansfelder Kupfer und Messing GmbH trägt ab diesem Datum den Namen KME Mansfeld GmbH. KME SE ist eine hundertprozentige Tochter der Intek Group S.p.A. mit Sitz in Mailand. |
Literatur
Beiträge im Mansfed-Echo:
- Geschichte der Lackdrahtfabrik im Walzwerk Hettstedt (Teil I)
- Geschichte der Lackdrahtfabrik im Walzwerk Hettstedt (Teil II)
- 100 Jahre Walzwerk Hettstedt / Teil I
- 100 Jahre Walzwerk Hettstedt / Teil II
MANSFELD Die Geschichte des Berg- und Hüttenwesens, Band II
(Letzte Aktualisierung: Mai 2022)
Bildergalerie