GESCHICHTLICHE ENTWICKLUNG DES MANSFELDER BERGBAUES
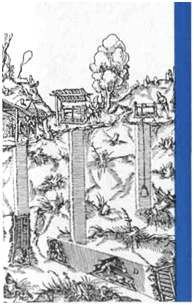
„Agricola, De re metallica",
Basel 1556
Kupferschiefer, dieses unscheinbare und doch so wertvolle Erz, bildet die Grundlage und den Reichtum unseres heimischen Bergbaues und unserer Hüttenindustrie. Diese schwarze schiefrige Gesteinslage von 20 bis 30 cm Mächtigkeit hat eine sehr mannigfaltige Zusammensetzung, Neben dem Kupfer, von dem dieses schwarze Gestein seinen Namen erhielt, sind noch viele andere Buntmetalle vertreten, vor allem Blei, Zink, Nickel, Silber und auch Gold. Diese reichhaltige Zusammensetzung - insgesamt sind über 50 Elemente nachgewiesen - war schon sehr frühzeitig die Ursache für die Entwicklung des Bergbaues und Hüttenwesens. Nach Angaben des ältesten Chronisten der ehemaligen Grafschaft Mansfeld, Cyracius Spangenberg, soll der Anfang des Mansfelder Bergbaues auf das Jahr 1199 zurückzuführen sein, in dem der Bergbau auf dem Kupferberg bei Hettstedt von den beiden Bergleuten Nappian und Neuke begonnen worden sein soll. Rings um die Mansfelder Mulde sind jedoch Funde von Steinwerkzeugen auf alten Schmelzhalden gemacht worden, und auch die Bronze-und Edelmetallgegenstände in den Fürstengräbern der Bronzezeit beweisen, daß schon in prähistorischer Zeit im Mansfelder Raum Kupfer gewonnen wurde, zu dessen Herstellung die Menschen jener Zeit die verwitterten grün und blau gefärbten Kupfererze und das rote metallische Kupfer am Ausgehenden des Flözes verwendet haben mögen. Um die Wende des 14. Jahrhunderts erlangte der Bergbau an zahlreichen Stellen am Ausgehenden des Flözes im östlichen Vorharz, insbesondere in der Gegend von Mansfeld, Hettstedt und Sangerhausen, eine hohe Blüte, Ganz Europa westlich der Elbe wurde damals mit Mansfelder Kupfer versorgt. Dieses Kupfer war für die damaligen Herren des Mansfelder Landes eine Quelle von Reichtum und Macht. Sie verkauften das Kupfer und Silber möglichst teuer, stritten sich um seinen Besitz und verwandelten den Schweiß der Berg- und Hüttenleute in Gewinn. In den kriegerischen Wirren des 16. und 17. Jahrhunderts trat ein allmählicher Verfall des so blühenden Mansfelder Bergbaues ein, und im Dreißigjährigen Krieg kam er ganz zum Erliegen. Erst nach der Freierklärung des Bergbaues im Jahre 1671 war eine langsame Wiederbelebung festzustellen.
Die Napoleonischen Kriege zu Beginn des 19. Jahrhunderts brachten jedoch neue Schwierigkeiten und den Bergleuten neue Lasten. Es ist daher nicht verwunderlich, daß viele Mansfelder Berg- und Hüttenleute als Freiwillige des Mansfelder Pionier-Bataillons teilnahmen an dem Befreiungskampf der Völker vom napoleonischen Joch. Die Opferbereitschaft und der hohe Patriotismus wurden von den Herren der Mansfelder Gewerkschaften jedoch nicht gelohnt.
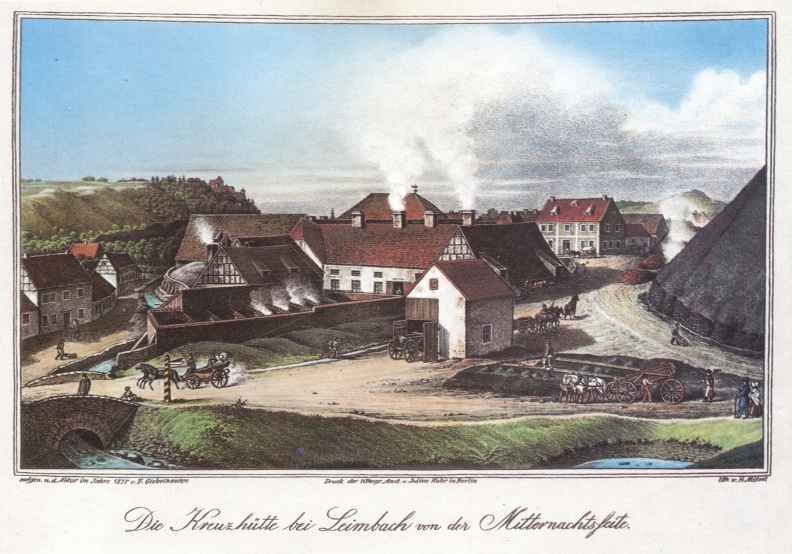
Im Jahre 1852 schlossen sich die fünf bis dahin bestehenden Gewerkschaften zu einer einzigen „Mansfeldischen Kupferschieferbauenden Gewerkschaft" zusammen. Damit war ein für die damalige Zeit riesenhafter Betrieb entstanden, das größte Industrieunternehmen Mitteldeutschlands. Eine neue Aufwärtsentwicklung begann. Umfangreiche Schachtanlagen, Wasserhaltungen und leistungsfähige Hüttenwerke wurden gebaut. Die um die Jahrhundertwende begonnene technische Entwicklung hatte die Mansfelder Schachtanlagen zu den größten Erzbergwerken der Welt gemocht.
Im Gegensatz dazu wurden die Sicherheitsmaßnahmen, die sozialen Einrichtungen, wie Waschkauen, Sanitätsstellen und Küchen vernachlässigt. Die Sorge um den Menschen spielte in dem Profitbestreben der Kapitalisten nur eine untergeordnete Rolle. Das Leben der Bergarbeiter war entbehrungsreich und hart. Schon in frühester Jugend mußten die Kinder der Bergleute mit hinzuverdienen, und von der Schulbank weg gingen die vierzehnjährigen Jungen auf den Schacht und arbeiteten unter Tage. Der Schichtlohn für einen Häuer betrug 2,40 RM, Es entwickelten sich harte Kämpfe der Arbeiter des Mansfelder Landes gegen diese kapitalistische Ausbeutung. Der Streik im Jahre 1909 brachte im Bewußtsein und in der Haltung der Mansfelder Bergarbeiter eine große Wende, Nach jahrhundertelanger Unterdrückung und Ausbeutung stellten sich die Bergarbeiter zum ersten mal im offenen Kampf gegen die Unterdrücker, Dieser revolutionäre Geist bewies sich in den ruhmreichen Kämpfen der Eislebener Bergarbeiter ganz besonders in der Zeit von 1917 bis 1921.
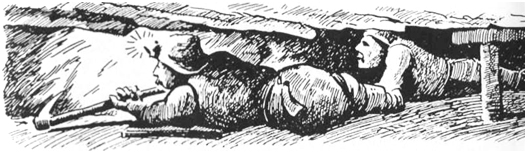
Die „Mansfelder Kupferschieferbauende Gewerkschaft" wandelte sich im Jahre 1921 in eine „Mansfeld Aktiengesellschaft für Bergbau und Hüttenbetrieb" um, die außer dem heimischen Kupferschiefer- und Erzbergbau auch Braunkohlen-, Steinkohlen- und Kalibergbau umfaßte, Da in der krisenreichen Zeit nach dem ersten Weltkrieg bei den damals herrschenden Weltmarktpreisen für Kupfer eine Lebensfähigkeit dieses privatwirtschaftlichen Unternehmens ohne staatliche Zuschüsse nicht möglich war, wurde der Kupferbergbau von den übrigen Betrieben der Mansfeld A. G. getrennt und in einer besonderen Gesellschaft, der „Mansfelder Kupferschieferbergbau A. G." zusammengefaßt, die staatliche Stützungen erhielt und unter staatlicher Kontrolle arbeitete. Diese finanzkapitalistische Maßnahme war typisch für das Wesen des Kapitalismus, dessen Hauptziel die Erzielung von Maximalprofit ist. Die rentablen Betriebe, die hohe Profite und Dividende für die Aktionäre abwarfen, wurden zu einem Konzern in den Händen des Monopolkapitals vereinigt. Gleichzeitig schloß man die weniger rentablen Betriebe gesondert zusammen und unterstützte sie mit Subventionen, die aus dem Steueraufkommen des Volkes kamen. Die Werktätigen trugen damit die Lasten der unrentablen Betriebe und bezahlten so aus ihrer Tasche die Dividende der Aktionäre, die den Profit der rentablen Betriebe einstrichen.
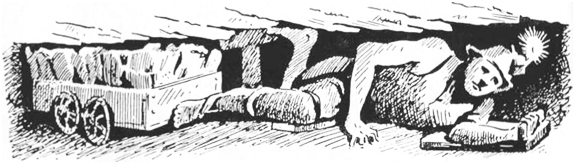
Nach dem zweiten Weltkrieg gingen die Betriebe des Mansfelder Kupferschieferbergbaues und die Hütten in die Hände des Volkes über. Ein gewaltiger Umwandlungsprozeß vollzog sich. Die revolutionäre Kraft der Arbeiterklasse konnte sich in vollem Umfang entfalten. Aus einem neuen, sozialistischen Bewußtsein heraus erwachsen täglich neue Kräfte, die die Entwicklung unaufhaltsam weitertreiben. Die Legende vom sterbenden Mansfelder Bergbau wurde eindeutig widerlegt. In den bestehenden Betrieben wurden umfangreiche Investitionen durchgeführt, die zu einer wesentlichen Leistungssteigerung von der Gewinnung bis zur Verarbeitung geführt haben. Dank der großzügigen geologischen Erkundungsarbeiten im Sangerhäuser Revier konnten neue Abbaufelder mit hohen Kupfergehalten erschlossen werden. Da die Kupfergehalte in der Mansfelder Mulde nach dem Muldentiefsten hin zugunsten höherer Blei- und Zinkgehalte im Flöz abnehmen, verlagert sich der Abbau des Kupierschieferflözes langsam aus dem Mansfelder in das Sangerhäuser Revier.
Im Jahre 1951 förderte der Thomas-Münzer-Schacht in Sangerhausen das erste Kupfererz. 1952 wurde der Bau einer weiteren Großschachtanlage in Niederröblingen begonnen. Heute bereits sind diese Schächte die wichtigsten Betriebe unseres Kombinates geworden. Die bisher erschlossenen Lagerstättenvorräte sichern den Abbau für die nächsten 50 Jahre, doch bei der Weiterführung der geologischen Erkundung zeichnet sich eine weitere Zunahme dieser Vorräte ab.
DIE LAGERSTÄTTE
Der Gegenstand des Mansfelder Bergbaues ist der vererzte Kupferschiefer und sein unmittelbares Hangendes im südöstlichen Harzvorland.
Begrenzt wird das Bergbaugebiet durch die Halle-Hettstedter Gebirgsbrücke im Osten, durch den Harz im Norden, den Kyffhäuser und die Finnestörung im Westen und Südwesten und durch den Rand der Querfurter Mulde im Südosten. Der Hornburger Sattel trennt das gesamte Gebiet in die Teillagerstätten der Mansfelder Mulde und des Sangerhäuser Reviers. Der Kupferschiefer ist darüber hinaus in ganz Norddeutschland bis zu den Rändern der alten Gebirge (Rheinisches Schiefergebirge, Thüringer Wald) verbreitet, ist aber meistens nicht bzw. nur wenig vererzt.
Stratigraphisch ist der Kupferschiefer als zweitunterstes Schichtglied an die Basis des Zechsteins, der unteren Abteilung der Permformation, zu stellen. (Siehe Schnitt.) Der Zechstein wird unmittelbar unterlagert von den roten Sandsteinen. Schiefertonen und Konglomeraten des Rotliegenden, die aus Abtragungsschutt entstanden sind. Das eindringende Zechsteinmeer arbeitete die obersten Partien dieser Sedimente zum Weißliegenden, einem gleichmäßig gekörnten grauen Sandstein, bzw. zum Zechsteinkonglomerat um. Darüber lagerte sich in einem vom offenen Meer abgeschnürten Becken Faulschlamm ob, der uns heute verfestigt als Kupferschiefer vorliegt. Danach setzte das Meer den Zechsteinkalk ob, dessen Neugliederung aus der Abbildung hervorgeht (die Zonen Bankkalk bis Anhydritischer Kalk entsprechen dem „Zechstein" der Bergleute). Der überlagernde Untere Werraanhydrit ist bei fortschreitender Verdunstung ausgeschieden worden und leitet somit zu den Steinsalz- und Kalisalzablagerungen über. Das gesamte Schichtenpaket ist in einem relativ trockenen Klima entstanden.
Heute fällt das Kupferschieferflöz in der Mansfelder Mulde mit etwa 5° zum Zentrum hin ein. Am Nord- und Südrand ist das Einfallen jedoch steiler. Die geologischen Störungen streichen generell Westnordwest-Ostsüdost. Die Mansfelder Mulde läßt sich nach dem Grad der Gestörtheit in einen fast ungestörten Südteil, einen mittleren Teil mit Störungen kleinerer Sprunghöhe und einen Nordteil mit Störungen größerer Sprunghöhe unterteilen; jedoch sind auch im Nordteil Störungen geringerer Sprunghöhe vorhanden. Im Sangerhäuser Revier Fällt das Flöz generell mit etwa 3° nach Südosten ein. Das Gebiet wird von Nordwest-Südost und Südwest-Nordost streichenden Störungen recht unterschiedlicher Sprunghöhe durchsetzt. Dadurch wurde das Gebiet in Schollen zerteilt (Bruchschollengebirge).
Vorherrschend ist die ebene Ablagerung des Flözes, unterbrochen wird sie in manchen Feldesteilen durch das gehäufte Auftreten von Weißliegend-„Dünen" (nach neueren Untersuchungen Strandwälle).
Der Kupferschiefer wird genauer als ein sulfidführender bituminöser Mergelschiefer bezeichnet. Vom Bergmann wird er seit alters her von unten nach oben In die (siehe Abb.)
- Feine Lette = Lage 1,
- Grobe Lette = Lage 2,
- Kammschale = Lage 3,
- Schieferkopf — Lage 4 und
- Schwaze Berge = Lage 5
eingeteilt.
Feine Lette und Grobe Lette sind durch die körnige oder Hiekennaht voneinander getrennt, auf der es zur Ausbildung von zahllosen winzigen Erdpechkügelchen kam. Die Kammschale ist nach unten durch die Feine Naht, noch oben durch die Grobe Naht abgegrenzt. Beide sind als Kalzit- bzw. Anhydritlagen oder auch als „Erzlineale" ausgebildet. Die Farbe nimmt von braunschwarz bis dunkelgrau nach oben ab, auch die Schiefrigkeit wird in dieser Richtung geringer, während die Härte zunimmt. Der überlagernde Dachklotz ist ein massiger Mergelkalk, die Fäule hingegen wäre als feinplattiger mürber Mergel zu bezeichnen. Die Ausbildung des Flözes und des Hangenden wird auf „Dünenkämmen" maximal bis auf die Lagen 1-4 reduziert, so daß Lage 5, Dachklotz und Fäule fehlen.
Der Kupferschiefer ist etwa wie folgt zusammengesetzt:
- 40 Prozent Kalkspat, Dolomit. Gips und Anhydrit,
- 5 Prozent Quarz,
- 7 Prozent Feldspat,
- 5 Prozent Kaolin,
- 2 Prozent Serizit,
- 29 Prozent Kieselsäuregel,
- 9 Prozent Bitumen und
- 2 Prozent Metallsulfide.
Der Bitumengehalt nimmt im Flöz noch oben ob, der Kalkgehalt nimmt zu. Das Liegende zeichnet sich durch hohen SiO2-Anteil aus. Der Kalkgeholt ist im Dachklotz und in der Fäule höher als im Flöz, was für den Hüttenprozeß von großer Bedeutung ist.
Die wichtigsten Erzmineralien sind
- Buntkupferkies,
- Kupferglanz,
- Kupferkies,
- Zinkblende und
- Bleiglanz.
Untergeordnet treten
- Pyrit,
- Markasit,
- ged. Silber und
- Fahlerz auf,
Kupfer, Blei und Zink sind die mengenmäßig bedeutendsten Metalle. Insgesamt sind im Kupferschiefer über 50 der bekannten Elemente des Periodensystems nachgewiesen worden, von denen besonders Silber, Nickel, Germanium, Selen und Rhenium wachsende wirtschaftliche Bedeutung besitzen. In den unteren Flözlagen sind die Erzmineralien in Form von feinen Stäubchen, der „Speise", oder in schichtparallelen schmalen Schnüren („Erzlinealen") ausgebildet. In den oberen Lagen und im vererzten Hangenden ist die Vererzung durch unregelmäßig begrenzte Körner, „Hieken" und „Bohnen", makroskopisch erkennbar. Die Kupfervererzung beschränkt sich im allgemeinen auf die unteren Flözlagen, reicht jedoch in der Nähe der Roten Fäule bis in die Schwarzen Berge und den Dachklotz. Rote Fäule ist eine Rotfärbung des Dachklotzes und der Fäule, teilweise auch des Flözes und des Bankkalkes. Sie ist pünktchen-, flecken- und bandförmig ausgebildet und durchsetzt die Lagerstätte inselförmig. Im Bereich der Roten Fäule ist kein Metallgehalt vorhanden. Blei und Zink sind überwiegend in den nicht kupfervererzten oberen Lagen ausgeschieden. Am Rande von Kupferfeldern schließen sich häufig Felder mit Blei-Zink-Vererzung der unteren Flözlagen an. Eine andere Form der Vererzung findet sich auf Störungen („edle Rücken"), die auch das Flöz, das Hangende teilweise bis zum Bankkalk, mitunter auch das Liegende beeinflußt. Durch höhertemperierte Lösungen wurden hauptsächlich Kupfer in den o. a. Mineralien, jedoch auch Kobalt-Nickel-Arsenide abgesetzt. Gangartmineralien sind Schwerspat, Kalkspat und Quarz.
Nach den neuesten Erkenntnissen ist der Metallgehalt des Flözes größtenteils durch Bakterien und deren Verwesungsprodukte (H2S) als Sulfid ausgefällt worden. Die Herkunft der Metallmengen ist noch nicht restlos geklärt. Sie können sowohl von Resten des varistischen Gebirges, die aus dem Zechsteinmeer herausragten, als auch von den unterlagernden Schuttmassen des Rotliegenden in gelöster Form in den Ablagerungsraum transportiert worden sein. Eventuell haben auch aus Magmagestein stammende hydrothermale Lösungen den Metallinhalt mit sich geführt und im Meer abgeschieden.
DIE GEWINNUNG
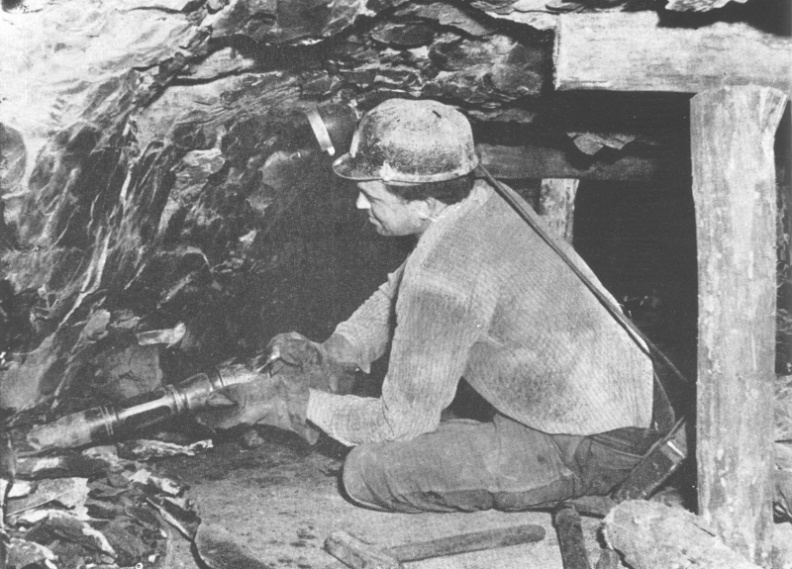
Die Gewinnung des Mansfelder Kupferschiefers geschieht zur Zeit auf drei Schachtanlagen in der Mansfelder Mulde und zwei Großschachtanlagen im Sangerhäuser Revier, Während in der Mansfelder Mulde zur Zeit zwischen der 7. und 13. Tiefbausohle in einer Teufe bis 1000 m unter der Erdoberfläche der Abbau des Kupferschiefers und der Abbau der Dachberge, vom Mansfelder Bergmann unter dem Sammelbegriff „Minern" zusammengefaßt, erfolgt, wird in der Schachtanlage Niederröblingen zwischen 8. und 10. Tiefbausohle bei einer Teufe bis 800 m mit dem Abbau begonnen.
Einen Überblick über Gewinnung und Forderung des Kupferschiefers zeigt das Schema eines Mansfelder Kupferschieferbergwerkes. Wie aus dem perspektivischen Schema ersichtlich, gelangt man vom Schachtfüllort durch einen kurzen Querschlag zur Hauptfördersohle, die im Streichen des Flözes nach beiden Seiten hin aufgefahren ist. Von dieser Sohlenstrecke aus führen in Abständen von rund 1000 m sogenannte Flachen zur nächsttieferen Sohlenstrecke, Die Sohlenabstände betragen 63 m in der Senkrechten. Die Flachen werden, dem Flözeinfallen von 4 bis 7° entsprechend, 500 bis 1000 m lang. Durch dieses Streckennetz wird die Lagerstätte für den Abbau vorbereitet, der aus der Sohlenstrecke heraus beginnt.
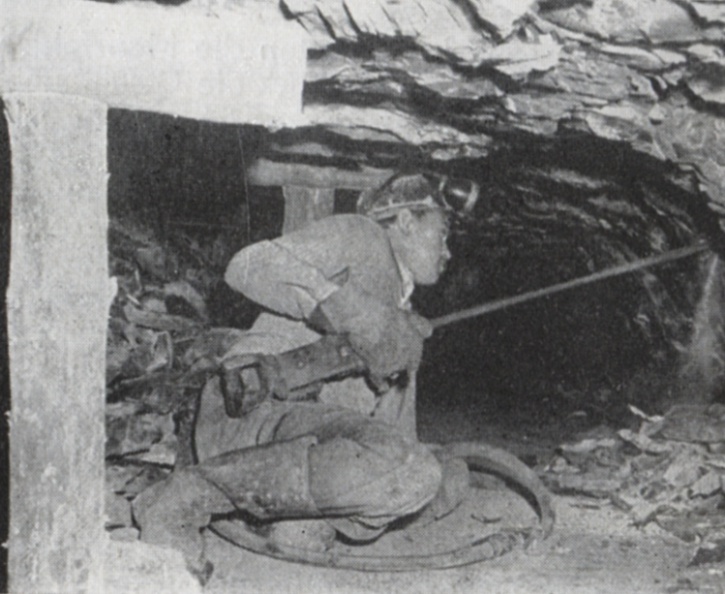
Die im Mansfelder Kupferschieferbergbau gebräuchliche Abbaumethode ist der Strebbau. Diese Abbauart erlaubt eine restlose Gewinnung des Erzes, Der Abbau wird in der Regel in der Sohlenstrecke begonnen, zunächst in einem schmalen Streifen streichend zu beiden Seiten der Sohlenstrecke durchgeführt und dann von der unteren zur oberen Sohlenstrecke, d, h., mit „schwebendem Verhieb" geführt. Der abgebaute Raum wird gut versetzt. Die Höhe des Abbauraumes, d.h. die 5trebhöhe. beträgt 0,30 bis 1,00 m, die Strebbreite zirka 2,00 m. In diesem Abbauraum ist der Hauer gezwungen, in kniender oder sitzender Stellung zu arbeiten.
Früher war diese Arbeit vor Streb noch bedeutend schwieriger. Der Mansfelder Bergmann mußte bei höchstens 0,50 m Strebhöhe die Schiefer auf der Seite liegend mit der Keilhaue heraushacken und in kleine Wagen, sogenannte Hunte, füllen, die dann von den Treckern am Fuß angebunden zur Strecke gezogen wurden. Die erzielbaren Leistungen waren sehr gering, jedoch wurden die Schiefern mit einer sehr hohen Reinheit gewonnen und nur reiche Flözpartien abgebaut.
Nach dem ersten Weltkrieg begann man mit der Einführung der Mechanisierung im Abbauraum, Zunächst wurden druckluftbetriebene Abbau- und Bohrhämmer eingesetzt. Die Förderung im Strebraum bzw. in der Förderfahrt wurde durch elektrische Haspel mit Seilförderung - sogenannter „elektrischer Junge" - und auf Schienen laufende Hunte ersetzt. Mit Hilfe des Drucklufthammers wird das Flöz herausgeschrämt, der Streb wird 40 bis 50 cm tief unterhackt. Die hangenden Berge werden abgebohrt und nach dem Abfördern der Schiefern in den Streb hereingeschossen. Diese Berge werden in den abgebauten Raum versetzt, nur die Berge, die nicht untergebracht werden können, werden nach über Tage gefördert. Eine andere Art der Gewinnung besteht in der vorhergehenden Hereingewinnung des über dem Flöz anstehenden tauben Materials durch Schießen und Hereinbrechen mit dem Abbauhammer und dem nachfolgenden Auflockern der so abgeräumten Schiefern. Mit kleinen Wagen, sogenannten Strebhunten, welche zirka 250 kg Fassungsvermögen besitzen und eine leicht kippbare Mulde haben, werden die Schiefern aus dem Flöz herausgefördert. In den sogenannten Strebfahrten, den in Strebhöhe im abgebauten und versetzten Raum ausgesparten Verbindungswegen zwischen dem Strebraum und den Abbaustrecken, erfolgt die Förderung mit elektrischen Haspeln. Auf der Sturzbühne werden die Schiefern aus dem Strebhunt in Grubenwagen mit einem Fassungsvermögen von 500 kg umgeladen und aus der Abbaustrecke über Bremsberge zu den Sohlenstrecken gefördert. In den Sohlenstrecken werden die Wagen zu Zügen zusammengestellt.
Nach wie vor erfolgt bei dieser Arbeitsweise die schwerste Arbeit, das Laden der Schiefern und Versetzen der tauben Berge, von Hand mit der kurzstieligen Handschaufel. Diese Arbeit hat in dem gleichen Maße zugenommen wie der Strebraum höher geschossen worden und die Verhiebsleistung in Quadratmeter gestiegen ist. Die durch Einführung der verschiedenen mechanisierten Geräte und durch eine straffere Betriebsorganisation erzielte Leistungssteigerung brachte einen Leistungsanstieg auf etwa 2,5 m2 freigelegte Flözfläche je Strebhauerschicht.
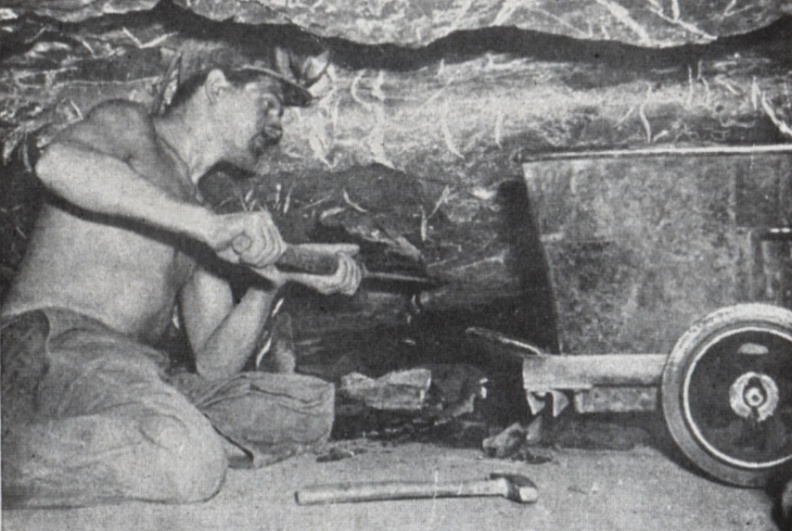
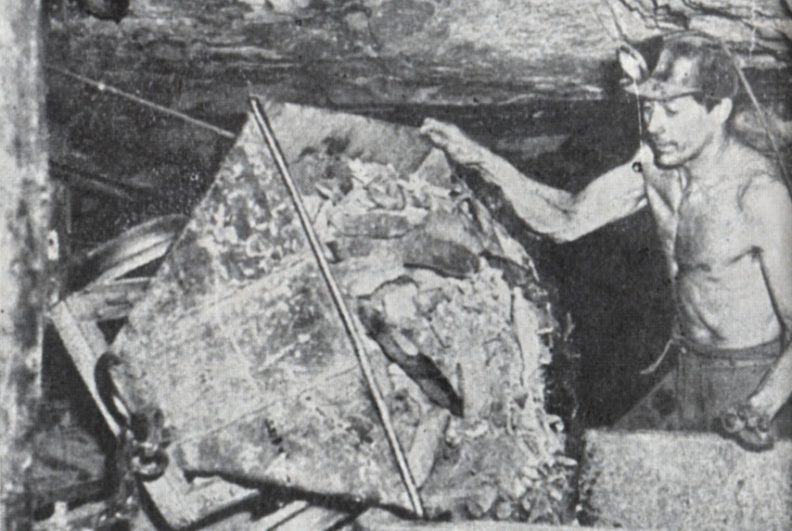
Schon sehr zeitig hatten die Mansfelder Bergleute erkannt, daß durch einen systematisch geregelten Gebirgsdruck die Gewinnungsarbeiten erleichtert werden können. Ohne Beachtung des Gebirgsdruckes ist das Kupferschieferflöz nur schwer gewinnbar. Durch den fortschreitenden Abbau wandert der aus den über dem Flöz lastenden Gebirgsmassen stammende Gebirgsdruck mit der Abbaufront vorwärts. Durch eine bogenförmig gestellte Verhaulinie wird der Gebirgsdruck so auf das Flöz gelenkt, daß dieses zermürbt und für die Gewinnung vorbereitet wird, Da das feste Liegende in der Regel nicht nachgibt, wird der den Strebstoß bildende Flözteil herausgepreßt und zermürbt. Dabei werden vorwiegend die eigentlichen Schieferlagen angegriffen, da auch die darüber liegenden Gesteinsschichten eine größere Festigkeit besitzen. Durch Absenkung der Dachschichten über dem zermürbten Flözteil kommen die Gebirgsdruckwirkungen auch in das Strebdach. Durch einen schnellen und gleichmäßigen Verhieb des Strebes wirken sich diese Erscheinungen jedoch erst über dem abgebauten Raum aus. Die bogenförmige Verhaulinie erlaubt, durch Veränderung des Bogenradius den Gebirgsdruck leicht zu lenken.
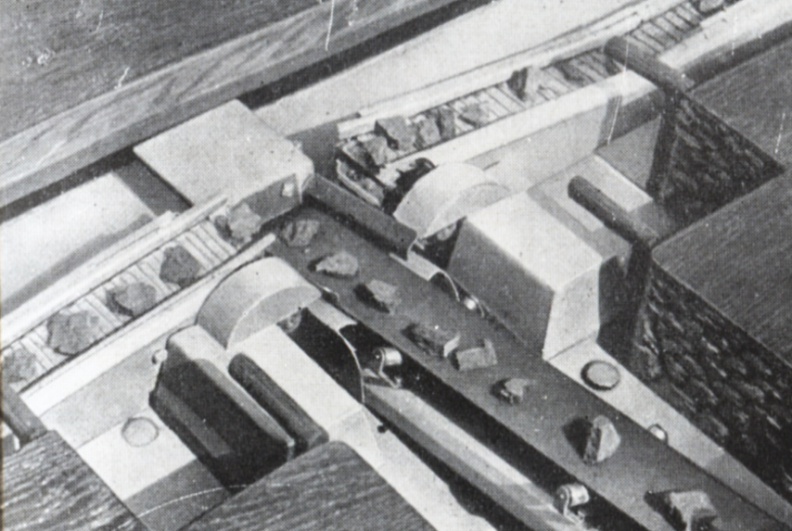
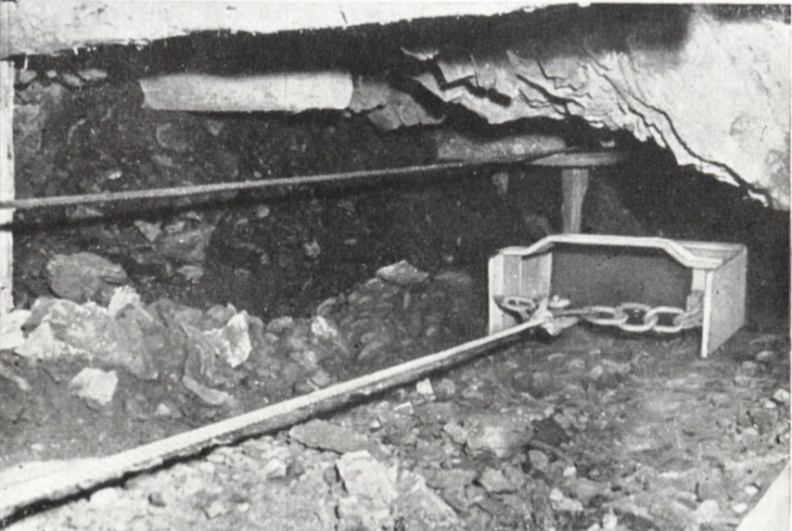
Lange Zeit verhinderte die bogenförmige Verhaulinie jede weitere Mechanisierung der Gewinnungsarbeiten vor Streb. Versuche mit Plattenbändern und Einschienenförderern vor Streb und Gummigurtförderern in bis vor Streb nachgeführten Bandbergen brachten gewisse Erfolge und führten zur Einführung dieser Geräte. Doch konnten hiermit nur die reinen Förderarbeiten mechanisiert werden. Lade- und Versatzarbeit erfolgt nach wie vor von Hand. Als weiteres Verfahren entwickelte sich daraufhin das Geradestrebabbauverfahren, Durch das Abgehen von der gebogenen Verhaulinienführung war der Einsatz von Schrappern im Streb möglich. Damit läßt sich die Ladearbeit ebenfalls mechanisieren. Mit Hilfe des vollmechanisierten Geradstrebes sollen auch die Versatzarbeiten, die beim Geradstrebabbauverfahren fast 50 Prozent der gesamten Arbeiten ausmachen, mechanisiert werden. Die Gewinnung der Schiefern erfolgt beim Geradstrebabbauverfahren durch Schießarbeit. Das Bohren wird mit Bohrwagen durchgeführt,
Durch die Schießarbeit treten hohe Gewinnungsverluste und Erzverdünnungen ein, die naturgemäß die Betriebskosten negativ beeinflussen. Deshalb werden zur Zeit Forschungsarbeiten durchgeführt, die sich einmal mit der Reduzierung der erwähnten negativen Faktoren beschäftigen, zum anderen die Entwicklung eines völlig neuen Abbauverfahrens zum Ziele haben. Das neuzuentwickelnde Verfahren wird als Blockrückbau mit Versatz bezeichnet. Durch Hochdrucktränkung soll die Festigkeit der Schiefern so weit herabgesetzt werden (Auflockerung im Vorfeld), daß eine anschließende schälende oder reißende Gewinnung des Flözes durch Schälschrapper bzw. Hobel möglich wird. Dabei wird das Nebengestein nicht mitgenommen (mannloser Streb). Als Versatz wird das aus dem Streckenvortrieb gewonnene Bergematerial im Blasversatzverfahren eingebracht. Die umfangreichen Versuche sind in der Bergbauforschungsabteilung angelaufen und werden Ende 1965 zum Abschluß gebracht.
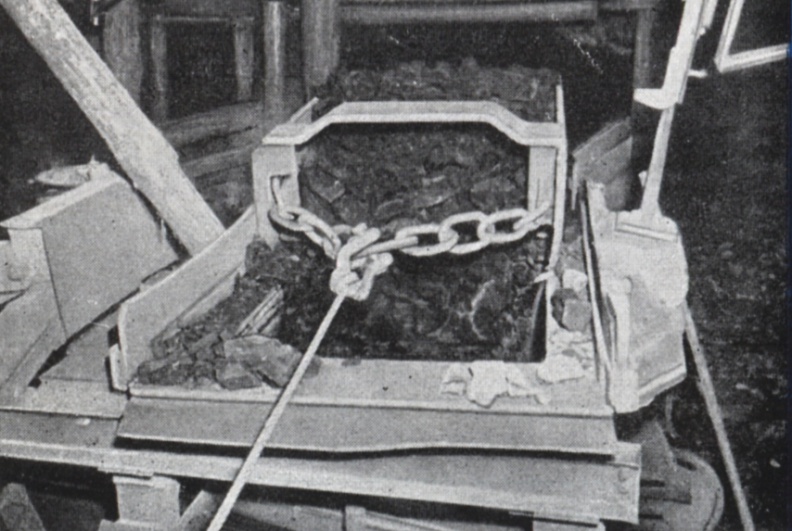
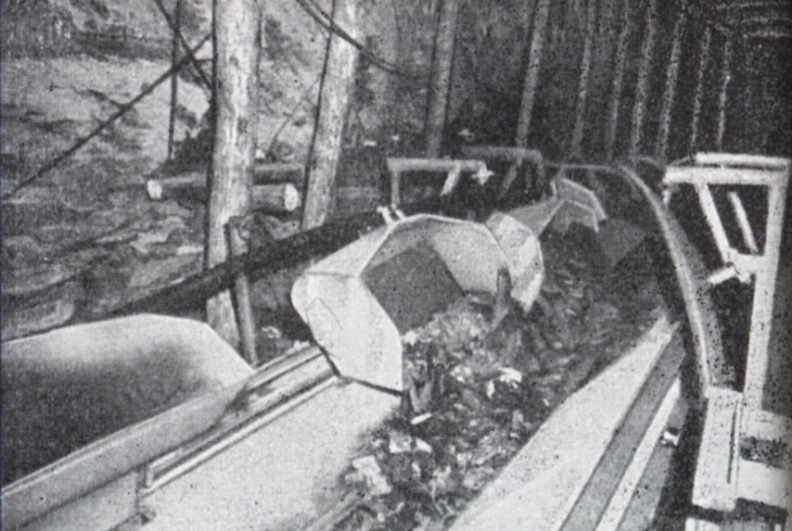
DIE FÖRDERUNG
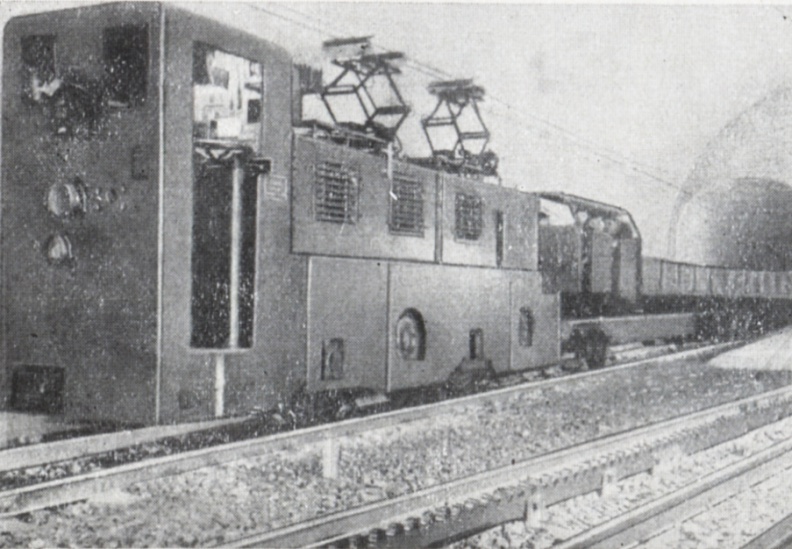
Die in den Sohlen zusammengestellten Züge werden mit Seilbahn oder E-Loks zu den Flachen gebracht. Auf überhöhten Rampen laufen die Wagen selbsttätig dem Flachen zu. Mittels Seilbahnanlagen mit modernen Schuhkettenmaschinen gelangen die Förderwagen durch die Flachen zur Hauptfördersohle, um hier mit E-Loks zum Schachtfüllort gefahren zu werden. Die Förderung in den Flachen erfordert einen hohen Arbeitskräfteaufwand und einen großen Bestand an Förderwagen zum gleichmäßigen Behang der Flachen. Außerdem brauchen die Strebbelegschaften viel Zeit, bis sie ihren Arbeitsplatz erreichen, und die Fahrung in den Flachen strengt an. So wurden zunächst Seilbahnen für Personenförderung gebaut, um die Wegzeiten zu verkürzen. Heute bringen auf dem Fortschrittschacht elektrische Zahnradbahnlokomotiven von 170 kW Leistung die Förderung aus der 13. Tiefbausohle zur Hauptförderstrecke und transportieren die Bergleute in Personenzügen bis zu ihrem Arbeitsplatz. Auf dem Otto-Brosowski-Schacht löst ein 2,6 km langer Querschlag vom Schacht zu den Bau-Feldern dieses Förderproblem. Die Schächte sind mit leistungsfähigen Schachtfördermaschinen ausgerüstet. Entsprechend der großen Teufe der Schächte wird auf allen Hauptschachtanlagen Treibscheibenförderung (Koepeförderung) mit mehretagigen Gestellen angewendet. Das Beschicken der Fördergestelle ist weitestgehend mechanisiert und die schwere körperliche Arbeit am Schacht unter und über Tage ausgeschaltet.
Durch entsprechende Signal- und Sicherheitseinrichtungen wird die Sicherheit der Bergleute gewährleistet. Alle Maßnahmen unterliegen der Kontrolle der Sicherheitsinspektion. Die Sorge um die Sicherheit und Gesundheit der Menschen ist oberstes Gebot bei allen Arbeiten, Jährlich werden große Mittel für Arbeitsschutz und technische Sicherheit in unseren Schächten aufgewendet.
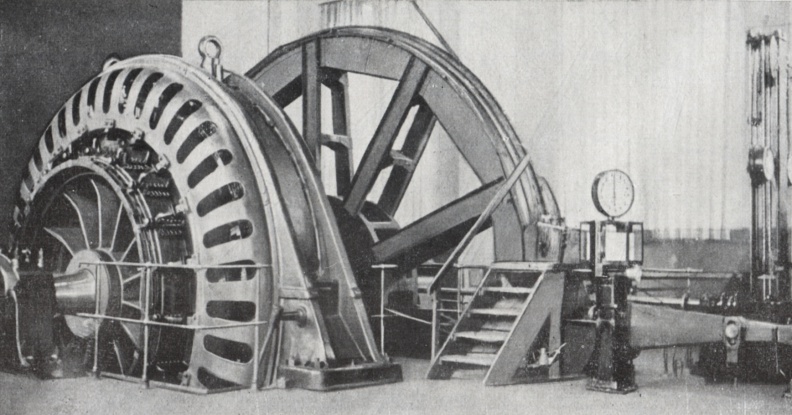
DER ÜBERTAGEBETRIEB
Zu jeder Schachtanlage gehören umfangreiche Übertageanlagen.
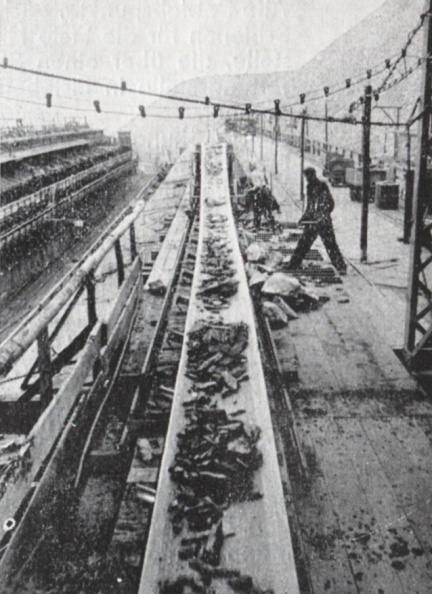
Die geförderten Schiefern wurden früher, getrennt nach den einzelnen Gewinnungsbrigaden in einzelne Kläubeställe gekippt und einer Handscheidung unterworfen, wo taubes Gestein von den Schiefern getrennt wurde und eine Kontrolle der Qualität der Arbeit der Gewinnungsbrigaden erfolgte. Diese Arbeit wurde von älteren, zur Grubenarbeit nicht mehr tauglichen Hauern oder Frauen durchgeführt. Der Kläuber spaltete die ihm als unschmelzwürdig bezeichneten Lagen ab, die als Ausschläge auf besondere Halden gingen. Heute ist die schwere Arbeit des Ausfahrens der Förderwagen und das Kippen in die einzelnen Kläubeställe sowie das Klauben selbst weggefallen. Mit Bandanlagen werden die Schiefern in größere Sammelbunker gefördert und aus diesen in die Großraumwagen der Werksbahn verladen. Die Qualität der Schiefern wird für jede Brigade in Kommissionskläubeanlagen bestimmt. (siehe hierzu auch: Die Kläubung des Kupferschiefers von Dr. Hans-Joachim Langelüttich )
Die Mechanisierung unter Tage und besonders die Erhöhung des Strebraumes auf 0,80 bis 1,00 m hatte einen Anstieg des Anteiles der Bergeförderung an der Gesamtförderung der Schächte zur Folge. Daher machten sich auch im Haldenbetrieb Mechanisierungsmaßnahmen erforderlich. Heute sind die modernen Haldenförderer zu einem Wahrzeichen unserer Schächte geworden. Das taube Gestein wird unmittelbar in Schachtnähe in große Bunker gekippt, aus denen es in großräumige, kippbare Gondeln abgezogen und durch Seilbahnen in einer Höhe von 100 m über die alten Halden gestürzt wird. Damit wird eine hohe Betriebskonzentration und Betriebssicherheit erlangt.
Ein gut ausgerüsteter Werkstattbetrieb sorgt auf jeder Schachtanlage für die schnelle Reparatur von Maschinen und Geräten. Die fortschreitende Mechanisierung stellt an die Werkstätten erhöhte Anforderungen. Heute sind die Mechanisierungswerkstätten der Bergbaubetriebe in der Lage, Änderungen an den Mechanisierungsgeräten vorzunehmen und kleinere Geräte selbst zu bauen. Großreparaturen aller Art sowie Neubau von Anlagen werden darüber hinaus von einer Zentralwerkstatt durchgeführt.
Hochspannungsschaltanlagen und Kompressorenanlagen stehen über und unter Tage für die Energieversorgung der Schächte zur Verfügung. Moderne Waschkauen, in den neuen Schachtanlagen als Schwarz-Weiß-Kauen eingerichtet, dienen zum Umkleiden der Belegschaft, Sie besitzen die nötigen Wasch- und sonstigen sanitären Einrichtungen. Ein Verbindungsgang führt zum Kauengebäude, in dem auch die Räume für die Lampenstation, Selbstretterkontrolle und Kaffeeküche untergebracht sind, direkt zum Schacht, so daß die unter Tage Beschäftigten nicht erst auf dem Wege zum Schacht auf den Werkplatz gelangen, was besonders bei schlechtem Wetter von Bedeutung ist.
Alle Betriebspunkte, auch unter Tage, sind darüber hinaus mit Medikamenten, Binden und Schienen für die Erste Hilfe versehen. Jeder einzelne Schacht besitzt eine Grubenrettungsstelle, die über einen Stamm ausgebildeter Grubenwehrmänner verfügt. In der Bezirksrettungsstelle in Eisleben erfolgt die Ausbildung und ständige Weiterbildung der Wehrmänner.
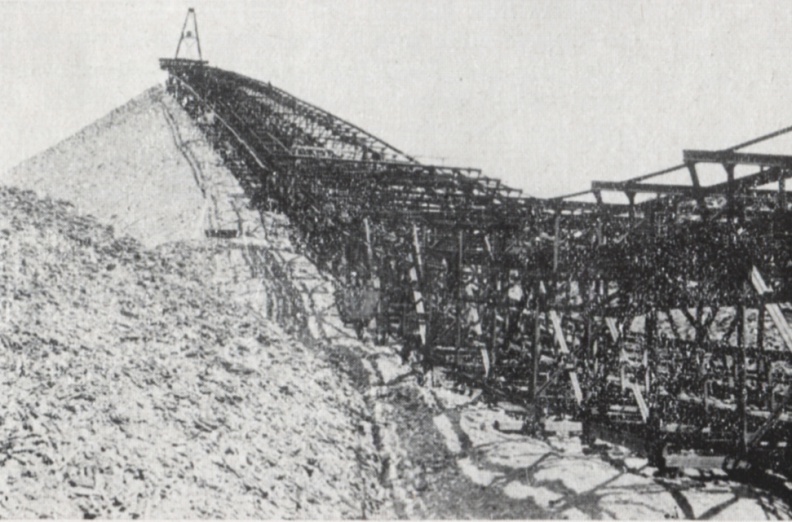
Zur Erhöhung der Alarmbereitschaft hat der VEB Funkwerk Dresden eine Alarmanlage entwickelt, die eine drahtlose Übermittlung eines Alarmrufes gestattet. Diese Anlagen bestehen im einzelnen aus der Fernbedienungseinrichtung, dem Sender und den Empfängern, Das Auslösen des Alarmes erfolgt an der Fernbedienung. Es ertönt im Empfänger ein intermittierender Ton, Zur Überprüfung der Anlagenbetriebsbereitschaft wird einmal täglich das Signal „Kontrolle“ gesendet. Das Auslösen dieses Signales erfolgt ebenfalls von der Fernbedienung und ruft im Empfänger einen Dauerton hervor. Der Empfänger ist ein 6-Röhren-10-Kreis-AM-5uper und arbeitet mit fest abgestimmtem HF-Bereich als Ein-Kanal-Empfänger. Unser Kombinat verfügt zur Zeit über zwei Sender. Der erste Sender alarmiert die Bereiche Thomas-Münzer-Schacht und Schachtanlage Niederröblingen. Dieser Sender ist auf dem Thomas-Münzer-Schacht stationiert. Der zweite Sender alarmiert die Bereiche Lademannschacht, Brosowskischacht und Fortschrittschacht, Die Bedienung dieses Senders erfolgt über den Hauptdispatcher von der Kombinatsleitung aus. Die Empfänger werden in den Wohnungen der Wehrmänner aufgestellt und bringen damit eine direkte Alarmierung. Dadurch entfällt die gegenseitige Verständigung mittels drahtgebundener Nachrichtenmittel bzw. die Verständigung von Mann zu Mann.
Beitrag eingestellt 01/2019