1. Einführung
Gegenstand des Beitrages sind Wesen und die Vielfalt der Probleme und Ihrer Lösungen in der Geschichte der Verhüttung des Mansfelder Kupferschiefers bis zur Gegenwart. Es wird ein Einblick in wesentliche Aspekte der die Entwicklung von metallurgischen Prozessen aus wirtschaftlicher und technischer Sicht gegeben. Ebenso wird aufgezeigt, welche Kenntnisse und Aggregate zum jeweiligen Zeitpunkt zur Verfügung standen und was die Hüttenleute zu Neuentwicklungen angetrieben hat. Die Übersicht ist prozessorientiert, um ein besseres Verständnis der Geschichte des Mansfeldischen Hüttenwesens zu ermöglichen, als das mit einer auf Standorte orientierten Betrachtung der Fall wäre.
Das Mansfelder Erz ist ein polymetallisches Erz, aus dem letztlich einmal 21 Metalle bzw. Elemente gewonnen wurden. Daraus ergibt sich die Notwendigkeit, die folgenden Betrachtungen auf die wesentlichen Arbeitsschritte und Produkte zu beschränken.
2. Die Anfänge im Mittelalter und die frühe Neuzeit
Kamerad Martin in der Mitte, links das Symbol der Bergleute und rechts das Symbol der Mansfelder Hüttenleute – so sieht das Logo zur 800 Jahrfeier des Mansfelder Kupferschieferbergbaus aus. Das Logo spiegelt kurz und prägnant die Realität der Beziehung zwischen Berg- und Hüttenleuten im Mansfeldischen wider. In der Frühzeit lagen hier in unseren Kupferschieferrevieren Bergbau und Hütte dicht beieinander. Transportwesen und Kommunikation waren nur wenig entwickelt. Nach Fall dieser Hemmnisse gingen Bergbau und Verhüttung besonders in der Neuzeit oft getrennte Wege. Nicht so im Mansfeldischen. Diese Besonderheit prägte unser Revier von Anfang an. Es lag einfach daran, dass das Kupferschiefer-Erz eben ganz spezielle Eigenschaften aufwies (Bild 1).
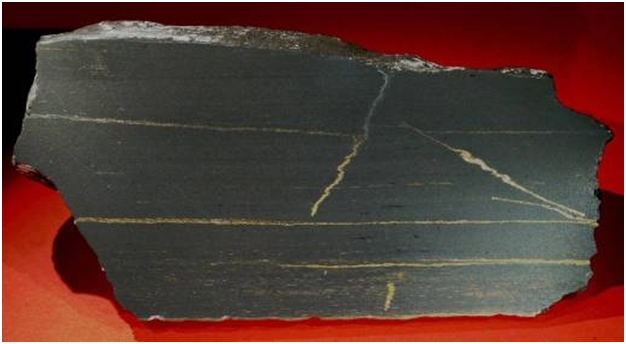
Die grauschwarzen Stellen sind Bitumenanreicherungen
(Fundort: Thomas Münzer-Schacht, Baufeld Brücken. Bildbreite ca. 14 cm, Foto Stedingk)
Mit der beginnenden Nutzung der Lagerstätte um 1200 waren die Mansfelder Bergleute vergleichsweise spät dran, wenn man daran denkt, dass sich die Verwendung von Kupfer schon 4000 v.Chr. nachweisen lässt. Doch diese Anfänge fußten auf der Kupfergewinnung aus Vorkommen von gediegenem Kupfer oder dessen karbonatischen Erzen. Was unsere Altvorderen hier gefunden hatten, war ein sulfidisches Erz mit 2 bis 3 % Kupfer, mechanisch praktisch nicht aufbereitbar, insbesondere wegen seiner hohen Bitumengehalte. Zum Glück enthielt das Erz auch noch 0,013 % Silber (entspricht auf Cu gerechnet ca. 0,5%) und war damit wirtschaftlich interessant. Seine Abtrennung stellte jedoch für den Hüttenmann über Jahrhunderte eine Herausforderung dar und wurde bis in die Neuzeit immer weiter verfeinert. Es stiegen die Ansprüche an die Technik hinsichtlich Ausbringen, Kosten, Schutz der Bedienungsmannschaften und der Umwelt. Und das alles zu jeder Zeit mit unterschiedlichen Möglichkeiten und Gewichtungen.
Das von ihm beschriebene Verfahren, später als „Deutscher Prozess“ bezeichnet, wurde recht lange angewandt. Erste Prozessstufe war das Abbrennen des Bitumens im Freien in Haufen von 50 bis 200 t (Bild. 2). Es folgten Röst- und Schmelzarbeiten, die schließlich zu metallischem Kupfer führten. Zum Schmelzen dienten niedrige Schachtöfen mit Spurzustellung und anschließendem Vorherd, so genannte „Krummöfen“ Der erste schmelzmetallurgische Schritt, nämlich das Konzentrationsschmelzen zur Herstellung eines Kupfersteines aus dem Erz, war bis in die Neuzeit prägend und kennzeichnet auch den „Mansfeld Prozess“. Das Konzentrationsschmelzen blieb immer Sache der Rohhütten. Der anfallende Kupferrohstein wurde in Stadeln geröstet. Das Röstgut, der „Rost“, stellte ein Gemisch von Kupfer- und Eisenoxiden dar, mit Resten an Sulfiden.
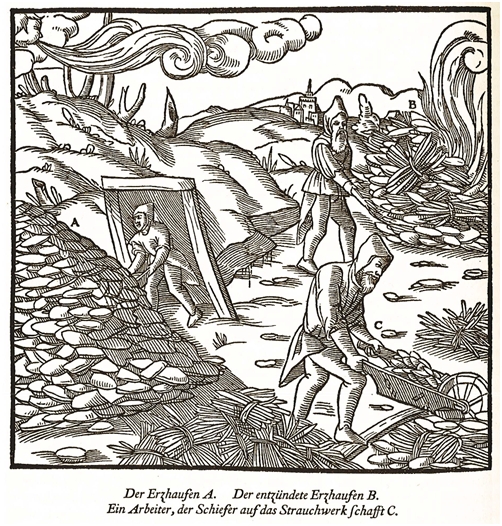
(aus AGRICOLA, Ausgabe 1928, S. 242)
Das Röstgut gelangte in die nächste Verarbeitungsstufe, dem Schmelzen im Schachtofen mit Holzkohle, später mit Koks. Erst der Schmelzprozess im Schachtofen trennte die Metalle von der Gangart, deren Bestandteile sich in der Schlacke sammelten.
Gerade die Prozessstufe „Schachtofen“ machte eine Reihe von Entwicklungen durch. Zu Anfang erhielt man noch keine richtige Schlacke, sondern eine halb gesinterte Masse. Die Öfen mussten von Hand beräumt werden. Mit besser werdender Technik (verbesserter Luftzufuhr durch Blasebälge) und immer besser werdendem metallurgischen Wissen (Zusatz von Schlackenbildnern) konnte der Prozess im Verlaufe der Zeit immer weiter verbessert werden.
Das dauerte jedoch seine Zeit. Schließlich kannte man die dem heutigen Hüttenmann bekannten Zustandsdiagramme noch nicht und musste probieren. So fand man auch heraus, dass es nicht nur wegen der relativ hohen Kupfergehalte der Schlacke günstig ist, Schlacke in den Schmelzprozess zurückzuführen. Diese Arbeitsweise nennt man „Rückschlacke“. Der Beschickung wird damit praktisch die „fertige“ Schlacke „gezeigt“. Solche Rückschlacke schmilzt besser als die Gangart und nimmt diese dann auf.
Erst später wurde es zum Allgemeinwissen des Hüttenmannes, dass die Bildungstemperatur der Schlacke höher ist, als ihre Schmelztemperatur. War also schon Schlacke da, war alles leichter. „Rückschlacke“ verbessert die Schmelzbarkeit und senkt den Metallgehalt der Schlacke. Natürlich hat man nicht die gesamte Schlacke im Kreis gefahren, nur solche mit hohen Metallgehalten. Hohe Temperaturen und eine gut flüssige Schlacke waren die technologischen Schlüssel zur Senkung der Metallverluste (Bild 3).
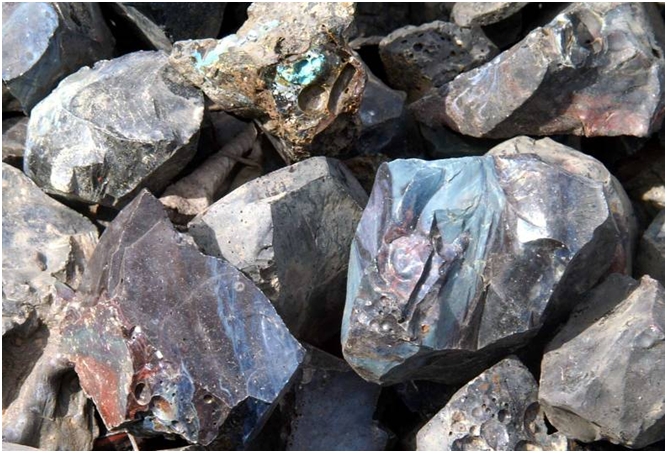
dass es im frühen 16. Jahrhunderts noch nicht gelang homogene metallarme Schlacken herzustellen.
Die Reste dieser Halde zeugen zugleich von der Tätigkeit des Vaters Martin Luthers (Hans Luder) als Hüttenmeister
(Foto Stedingk).
Das Kupfer aus den reduzierenden Schachtofenschmelzen enthielt neben Eisen, Nickel, Blei und Zink vor allem 0,5 bis 0,6 % Silber. Es war oft so, dass der Wert des Silbers den des Kupfers überstieg. Die Entsilberung des Kupfers war also dringend geboten.
In der Zeitachse der Geschichte sind wir jetzt an der Wende vom 15. zum 16. Jahrhundert. Um diese Zeit hatte man noch keine eleganten Verfahren zur Trennung von Kupfer und Silber. Man wusste aber um die Eigenschaften der Metalle, sich ineinander mehr oder weniger zu lösen und man wusste auch, dass diese Löslichkeit temperaturabhängig ist. Wenn man nun Metalle mit erheblichen Unterschieden im Schmelzpunkt hat, und diese in der flüssigen Phase mischbar sind, hat man eine Möglichkeit der Trennung unter Anwendung dieser Gegebenheiten.
Im Fall der Silberabtrennung ist es weiter von Vorteil, dass das niedrig schmelzende Metall Blei für Silber ein Sammler ist. Blei ist dafür schon lange bekannt. Solche Überlegungen bzw. Kenntnisse waren der Schlüssel für ein geeignetes Trennverfahren, das „Saigern“.
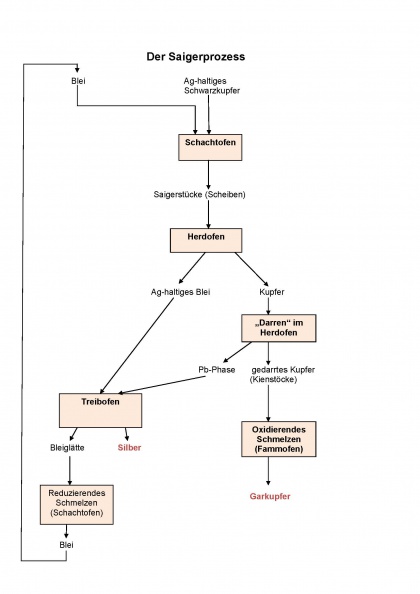
Man musste also zuerst eine homogene Schmelze aus Blei (Schmelzpunkt 327 °C) und Kupfer (Schmelzpunkt 1085 °C – hier weniger wegen der Verunreinigungen, die Schmelzpunkt erniedrigend wirken) herstellen. In praxi benötigte man hierfür Temperaturen über 1000°C. Das Zusammenschmelzen erfolgte in einem Schachtofen und man fand auch das Know-how, die notwendige Homogenität der Schmelze zu erhalten – angesichts der Schmelzpunktunterschiede und dem Wirkprinzip des Schachtofens eine Leistung.
Diese Schmelze wurde zu schweren Scheiben, den sogenannten Saigerscheiben oder -stücken, gegossen.
In einem 2. Arbeitsschritt wurden diese Saigerstücke erhitzt und zwar über den Schmelzpunkt des Bleis. Dabei lief – saigerte - das Blei aus und nahm das Silber mit. Das Saigerblei wurde im Treibofen in oxidierender Atmosphäre einer Temperatur von 1000°C ausgesetzt. Es bildete sich Bleioxid (Glätte), das die Verunreinigungen mit sich nahm und aus dem Herd lief. Nach der völligen „Verglättung“ blieb Silber mit 990 – 995 Feine zurück.
Das zurückbleibende Kupfer enthielt noch 20 – 30 % Pb und dementsprechend auch noch Silber. Im Interesse eines guten Silberausbringens war das unbefriedigend. Deshalb schloss sich eine weitere Verfahrensstufe an – das Darren. Das ist eine Temperaturbehandlung bei 900°C, wodurch der Pb-Gehalt auf 10 % zurückging. Dies „gedarrte“ Kupfer – Kienstöcke genannt – wurde oxidierend geschmolzen. Es entstand Mansfelder Garkupfer mit 0,6 % Pb.
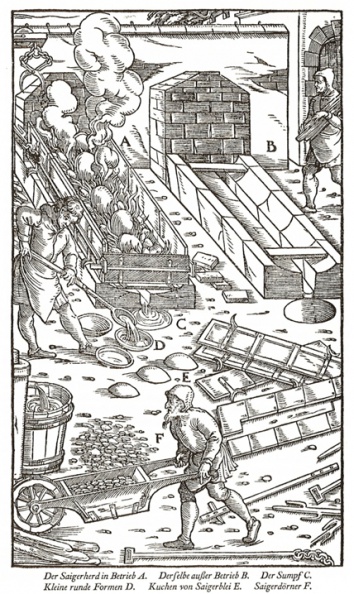
(aus AGRICOLA, Ausgabe 1928, S. 445)
3. Die Fortschritte des 19. Jahrhunderts
Der Saigerprozess war nicht billig. Er hat sich lange gehalten und es bedurfte der Fortschritte der Chemie der 1. Hälfte des 19. Jahrhunderts, bis man eine Alternative zu dieser Arbeitsweise gefunden hatte. Diese Neuerung war die Amalgation. Es kam also Quecksilber ins Spiel. Auf der Gottesbelohnungshütte wurde von 1825 bis 1827 das Amalgamierwerk gebaut. Das Gebäude ist – nebenbei gesagt – historisch und bis heute erhalten. Nach seinem Architekten wird es allgemein der „Schinkelbau“ genannt (Bild 6).
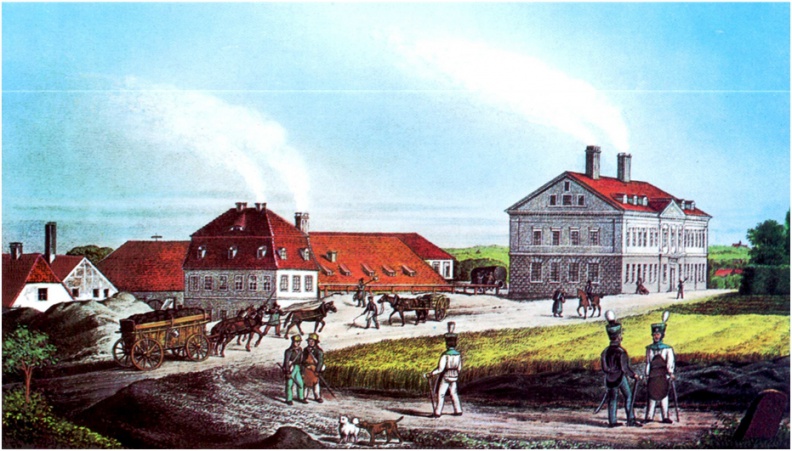
(Zeichnung Giebelhausen, Archiv Mansfeld Museum, Hettstedt)
Zur Amalgation war eine Vorstufe nötig. Vormaterial war natürlich weiter der Kupferstein, in dem das Silber als Sulfid vorliegt. Dieses muss zunächst in ein lösliches Silbersalz umgewandelt werden und zwar in Silberchlorid (Bild 7).
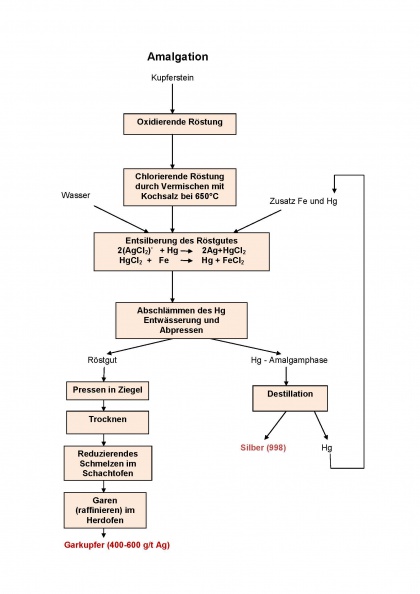
Hierzu wurde der Kupferstein zunächst einer oxidierenden - sulfatisierenden - Röstung und anschließend einer weiteren (chlorierenden) Röstung unterworfen. Dabei wurde das Röstgut mit Kochsalz vermischt und mit Wasser breiig angerührt und somit in diesem zweiten Schritt chlorierend geröstet. Bei 650 °C zerfallen die Sulfide des Eisens und des Kupfers in ihre Oxide. Dabei entsteht SO3. Dieses setzt aus dem Kochsalz Chlorid frei, welches das Silber in Silberchlorid umwandelt.
Das Röstgut wurde anschließend mit Quecksilber vermischt und metallisches Eisen zugesetzt. Es läuft dann folgende Reaktion ab: s.Bild 7
2 (AgCl2)- + Hg ==> 2 Ag + HgCl2
HgCl2 + Fe ==> Hg + FeCl2
Das Quecksilber stand damit zur Fortsetzung der Reaktion zur Verfügung, während das Silber vom Quecksilber gelöst (amalgamiert) wurde. Das entsilberte Röstgut wurde von Quecksilber abgeschlämmt, auf Nutschen entwässert und mit Ton und Kalk zu Ziegeln geformt und getrocknet. Die Ziegel wurden im Schachtofen auf ein Kupfer mit ca. 90% Cu verschmolzen, das in Herden gegart – raffiniert – wurde. Das so gewonnene Garkupfer enthielt noch 400 bis 600 g/t Silber – also mehr als das Saigerkupfer, weshalb auch weiterhin gesaigert werden musste. Auch reichte die Kapazität des Amalgamierwerkes nicht aus.
Das Quecksilber enthielt 0,7 % Silber und das Silberamalgam ließ sich abpressen. Das Silberamalgam wurde destilliert und es blieb ein relativ reines Silber (998 Feine) zurück.
Schon wegen der relativ hohen Silbergehalte im Garkupfer war man auch mit dem Amalgationsverfahren nicht so recht glücklich. Auch die belastende Arbeit mit Quecksilber war ein Nachteil. Also musste weiter nach Alternativen gesucht werden, die schließlich der damalige Leiter des Amalgamierwerkes, Augustin, fand.
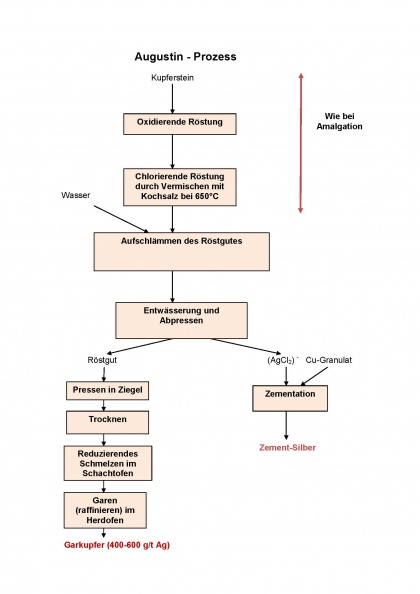
Er umging den Zementationsvorgang mit Quecksilber. Es blieb aber wie beim Amalgamierverfahren bei der chlorierenden Röstung. Nach einer Aufschlämmung des Röstgutes wurde die Silberchloridlösung abfiltriert. Das Silber wurde nun mit Kupfergranalien auszementiert. Durch Gegenstromführung von Lauge und Kupfergranulat gelang es einerseits, ein kupferfreies Zementsilber und andererseits eine entsilberte Lauge zu erzeugen, die nach der Auszementation des Kupfers mit Eisen abgeschlagen werden konnte. Die entsilberten Laugerückstände (aus dem Röstgut) wurden wie bei der Amalgation weiter verarbeitet.
Der Augustinprozess ermöglichte Ende 1843 zwar die Einstellung der Saigerung, beseitigte aber den Nachteil des Amalgationsverfahrens – die Silberverluste – nicht, auch wenn diese vergleichsweise zum Amalgationsverfahren etwas geringer waren. Und wieder inspirierte das zunehmende Wissen in der Chemie und über das Rösten zu einer Neuentwicklung – dem Ziervogelprozess.
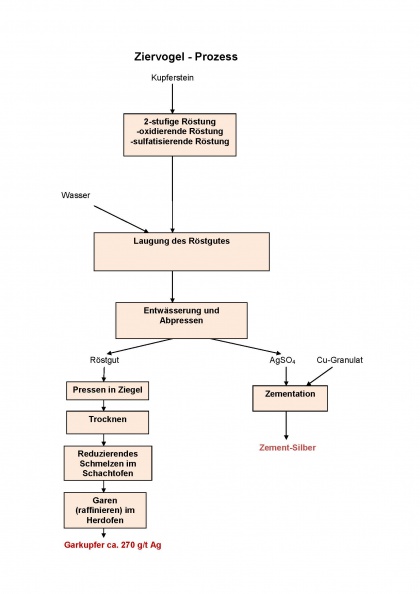
Die Entwicklung dieses Verfahrens wurde von der Tatsache befördert, dass sich in der ersten Röststufe bei der Amalgation (sulfatisierende Röstung) neben Kupfer- und Eisensulfat zum Teil auch Silbersulfat bildete. Dieses ist in heißem Wasser - wenn auch nicht besonders gut - löslich.
Man musste also in der Röstung erreichen, dass die Sulfatisierung des Silbers vollständig erfolgte. Das gelang, indem man die erste Röstung heißer führte, wobei sich die Sulfate zum größten Teil wieder in Oxide zersetzen. In einer zweiten Stufe wurde die Temperatur auf 900 bis 950°C erhöht. Jetzt zersetzten sich auch die restlichen Sulfate. Das frei werdende SO3 überführte das in der ersten Röstung entstandene metallische Silber sowie restliches Silbersulfid in Silbersulfat (AgSO4).
Das hört sich alles einfach an, war es in Wirklichkeit aber nicht. Die Anforderungen an die exakte Temperaturführung waren hoch, die damaligen Messgeräte gelangten an ihre Grenzen. Auch störten Nebenbestandteile die Bildung des Silbersulfates, sodass die gelungene Röstung letztlich für den Erfolg des Ziervogelprozesses entscheidend war.
Das Röstgut wurde anschließend schwach schwefelsauer gelaugt. Die Weiterverarbeitung der Produkte erfolgte wie beim Augustinprozess. Das Silber hatte nach dem Einschmelzen eine Feine von 999 bis 999,5. Aber auch an der Verarbeitung der Laugerückstände musste im Interesse des Silberausbringens noch gearbeitet werden (Nachrösten, Laugen). Das damals so erzeugte Kupfer enthielt immer noch 270 g/t Silber.
Die oben genannte Entwicklung wurde natürlich von der Entwicklung der Erzverarbeitung in den Rohhütten (z. B. Kupferkammer, Eckhardhütte, Kreuzhütte, Mittelhütte) befeuert. Der Bergbau konnte zunehmend mehr Erz liefern. Die Leistung der Rohhütten stieg von 12.000 t Erzdurchsatz im Jahre 1820 auf 28.000 t im Jahre 1850, um dann mit einer erheblichen Steigerung innerhalb von 20 Jahren, also 1870, mit 155.000 t aufzuwarten.
Ermöglicht wurde die Leistungssteigerung der Rohhütten vor allen Dingen durch den Ersatz der Holzkohle durch Koks. Doch diese Umstellung war mehr als Holzkohle raus und Koks rein! Die Schachtofenkonstruktionen mussten verändert werden und zwar durch Verengung der Ofenschächte. Blasebälge konnten weder die nötige Windmenge und -geschwindigkeit aufbringen noch den Druckwiderstand der deutlich höheren Beschickungssäule überwinden. Inzwischen gab es aber leistungsfähige Gebläse.
Die Veränderungen an den Öfen erforderte ein langwieriges Experimentieren. Es dauerte fast 100 Jahre (!), ehe eine brauchbare Relation von Querschnitt in der Düsenebene, der Form des Schachtes und der Höhe der Beschickungssäule gefunden wurde. Innovation war also nicht nur bei der Entsilberung sondern auch auf den Rohhütten gefragt.
Und noch eines sei hier erwähnt: Man erkannte auch, dass auch die Rohhüttenschlacke als Wertprodukt genutzt werden konnte und stellte Blähschlacke - zunächst in glasiger Form - her. Aber erst, als man kristalline Schlacke durch langsame Abkühlung - Tempern - herstellen konnte, eignete sich die Blähschlacke hinreichend für Bauzwecke. Schließlich gelang es auch Pflastersteine herzustellen, die noch heute in ganz Mitteleuropa zu finden sind (Bild 10).
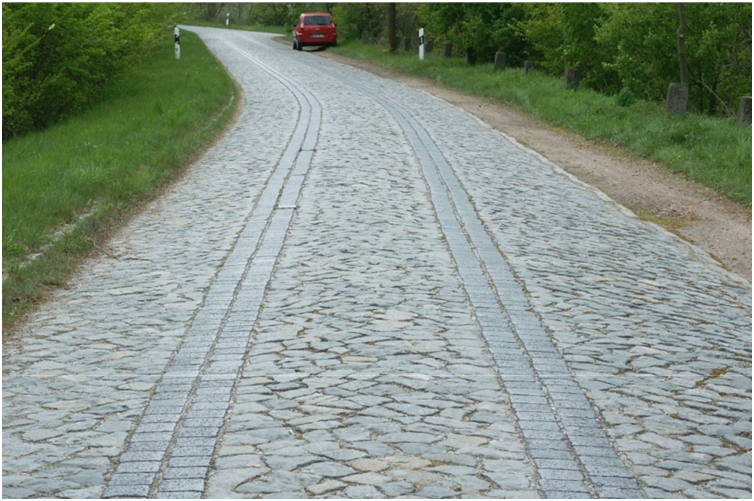
4. Das Entstehen von Großbetrieben und das moderne Hüttenwesen
Mit der Inbetriebnahme der ersten Tiefbau-Großschachtanlagen für die Förderung des Mansfelder Kupferschiefererzes in der Mitte des 19. Jahrhunderts wuchsen die Erzmengen deutlich an. So wurde die Errichtung neuer Hüttenkapazitäten notwendig, verbunden mit einer Konzentration der Verarbeitung des Erzes an wenigen Standorten. Die Kochhütte bei Helbra nahm im Oktober 1880 als zweite Großhütte ihren Betrieb auf, zehn Jahre nach der Krughütte bei Eisleben (Bild 11), was zur sukzessiven Stilllegung der alten Rohhütten führte.
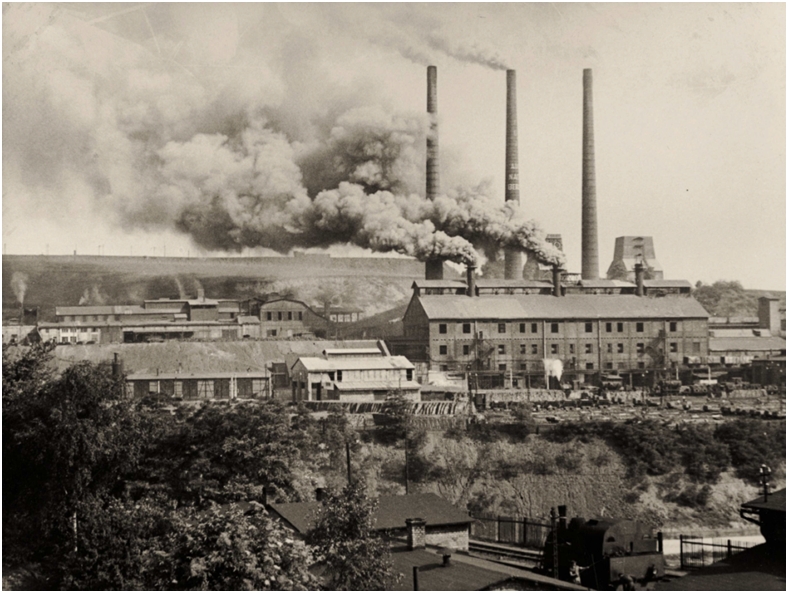
Die Umweltbelastung durch die Schwermetallemissionen dieser 1972 stillgelegten Hütte ist heute noch großräumig nachweisbar
(Foto Archiv Mansfeld Museum, Hettstedt), was aber grundsätzlich für alle Hüttenbetriebe auf der Welt gilt.
Indessen blieb es bei der althergebrachten Technologie der Erzverarbeitung: Schieferbrennen, Schmelzen auf Rohstein, Rösten, Herstellung von Rohkupfer mit Raffination auf Garkupfer. Dabei war das Rösten Sache der Rohhütten. Mit zunehmender Produktion konnte man die Röstgase jedoch nicht mehr unbehandelt lassen. Die steigende Produktion machte auch neue Rösttechniken erforderlich, mit Möglichkeiten zur Erfassung und Verwertung der Röstgase. Die Lösung waren die Mansfelder Kils, Röstschachtöfen, in ihrer Bauart ähnlich den Kalkbrennöfen.
Es ist eine traditionelle Arbeitsweise der Mansfelder Hüttenleute, die bis zum Schluss hochproblematisch war:
- Steinschmelzen an verschiedenen Stellen,
- Rösten an vielen verschiedenen Stellen,
- Kupfer-Herstellung aus Röstgut – auch an verschiedenen Stellen.
Geschuldet war dies, neben dem ständigen Probieren, auch dem Bestreben der Nachnutzung von abgeworfenen Standorten und Anlagen in modifizierter Form. Mit der Errichtung der beiden Rohhütten in Eisleben und Helbra wurde dann aber doch ein gewisser Konzentrationsprozess eingeleitet. Unter dem technologischen Druck der Rohhütten mit ihrer steigenden Kapazität wuchs darüber hinaus auch die Notwendigkeit grundsätzlicher Veränderungen im Gesamtprozess. Doch auch auf den Rohhütten waren zwingend neue Wege zu beschreiten. So war das Abbrennen der Schiefern im Freien nicht mehr tragbar und die Verarbeitung von ungebrannten Schiefern im Schachtofen geboten. Das „Brennen“ war aber bis dato unverzichtbar: Die Öfen „froren ein“, wenn dem nicht mit erhöhter Brennstoffgabe entgegen gewirkt wurde, was wiederum das Mauerwerk der Schachtöfen schmelzen ließ. Abhilfe konnte der Einsatz von Wassermantelöfen schaffen. In der Folge wurden die Wassermantelöfen Standard in der Rohhüttentechnologie. Für die Krughütte entschied man sich für die viereckige Bauweise, für die Kochhütte für die runde.
Metallurgisch ist die viereckige Form zu bevorzugen, wegen der Eindringtiefe der Luft, die runden Öfen im Durchmesser Grenzen setzt. Die Vergrößerung der Öfen hatte auch zur Folge, dass der Möller gut gasdurchlässig sein musste. Feines Material stört den Luftdurchfluss und führt zu Leistungsminderung. Das Feinmaterial musste also einen Prozess der Kornvergröberung durchlaufen. Das konnte durch Sintern oder Brikettieren erfolgen. Das Sintern ist für die Ofenführung besser, da es bei hohen Temperaturen stattfindet und somit die Schlacke schon vorformiert. Das Brikettieren ist einfacher und billiger und lässt auch keine nicht verwertbaren Abgase entstehen. Sintern war auf beiden Hütten im Einsatz, auf der Krughütte praktisch bis zum Schluss (1972), während auf der Kochhütte das Sintern durch eine Brikettierung abgelöst wurde. Gemeinsam hatten Krug- und Kochhütte im Endzustand Schachtöfen mit einem Vorherdbetrieb zur Trennung von Stein und Schlacke. Die Schlacke lief aus den Vorherden kontinuierlich in bereitstehende Schlackenwagen ab, der Rohstein wurde gesammelt und abgestochen. Anfangs in Sandbetten, später in Kokillen. In den Vorherden fand auch eine Abkühlung statt und diese bewirkte das Ausscheiden einer Eisenphase in fester Form aus dem flüssigen Rohstein – die sogenannte Eisensau. Diesen Fachbegriff sollte man etwas erklären: der Hüttenmann bezeichnet ungewollte aber trotzdem nicht zu verhindernde Ausscheidungen als „Sau“ (Bild 12).
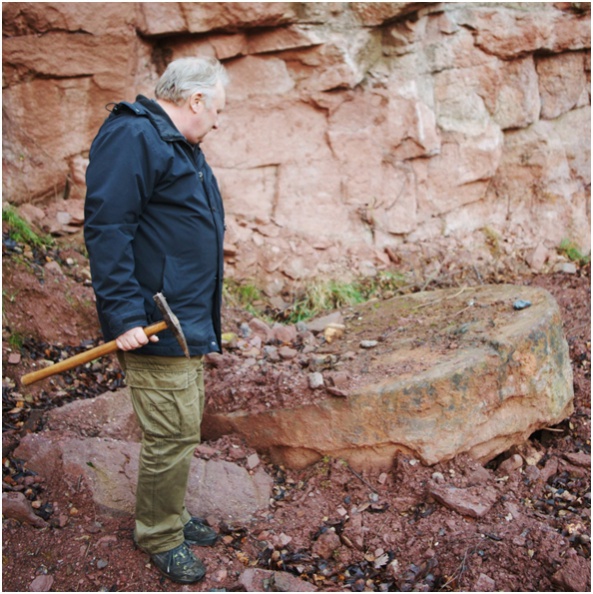
Durch die Bildung der Eisensau entstanden Kupferverluste. Aber es sammelten sich in ihr auch durchaus interessante Nebenelemente. Gerade diese machten sie bis in die siebziger Jahre des letzten Jahrhunderts immer wieder zu einem Forschungsobjekt. Letztlich gelang ihre Nutzung in den 1970er Jahren durch Einschleusung des Materials in den Laugeprozess der finnischen Kobalthütte Kokkola endgültig. Hierfür wurde die Eisensau in Helbra granuliert und an die o.g. Kobalthütte geliefert. Die Entstehung der Eisensau war auch insofern ein technologisches und damit auch wirtschaftliches Ärgernis, als dass sie die Vorherde nach und nach zu setzte, wodurch diese stillgelegt, abgebrochen und neu errichtet werden mussten. Somit waren zwei Vorherde für einen Ofen erforderlich, die intermittierend arbeiteten. Die Rohhüttenschlacke wurde zum großen Teil aufgehaldet, aber auch zu Schlackensteinen verarbeitet (Bild 13).
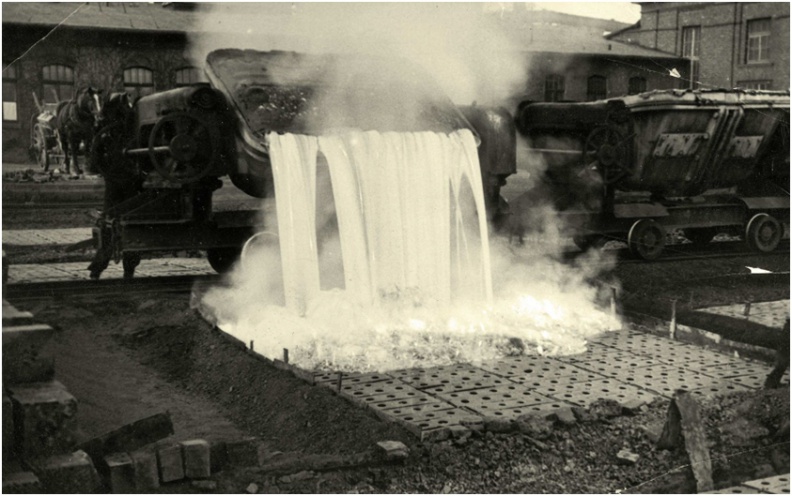
Auch die Abgase der Rohhüttenschachtöfen konnten nicht mehr unbehandelt ins Freie geleitet werden. Eine Reinigung war unumgänglich, gestaltete sich aber schwierig. Nicht zuletzt auch deshalb, weil das Brennen des Erzes zur Beseitigung des Bitumens aufgegeben worden war, sowohl aus Umweltgründen als auch unter wirtschaftlichen Gesichtspunkten (Bindung hoher Metallmengen).
Nun sind Bitumina aber schwere Kohlenwasserstoffe. Sie verdampfen im oberen Teil des Schachtofens und entweichen mit dem Abgas. Hinzu kommt, dass die im Vergleich zu früher viel forciertere Ofenführung hohe Temperaturen im Inneren der Öfen bedingt und die Ofenatmosphäre reduzierend ist. Das bedeutet, dass die mit dem Erz vorlaufenden, mengenmäßig nicht geringen Blei- und Zinkbestandteile verdampfen und letztlich vordergründig als Sulfide mit dem Abgas ausgetragen werden. Durch die besonderen Eigenschaften dieses so entstehenden Flugstaubes war die Gasreinigung eine echte Herausforderung. Besonders wegen des klebrigen Bitumens war nur eine Nassreinigung möglich. Hierfür zur Anwendung kamen die sogenannten Theissenwäscher, weshalb der ausgewaschene Flugstaub auch Theissenschlamm genannt wurde. Der Theissenschlamm war also, wie erläutert, auch ein Sammler für Blei, Zink und weitere interessante Nebenmetalle, sodass die „moderne“ Rohhütte letztlich folgende Produkte produzierte:
- Rohstein,
- Eisensau,
- Schlacke (Bauformsteine-Blähschlacke, Straßenbausteine),
- Theissenschlamm
- und ein Gichtgas mit hohen CO-Gehalten, das in nachgeschalteten Kraftwerken als Zusatzbrennstoff diente.
Die immer weiter steigenden Mengen an Rohstein erforderten auch neue Wege in der Rohsteinverarbeitung. Dazu bot sich in Anlehnung an die Stahlindustrie der Bessemer-Prozess an, dessen Eignung über Jahre untersucht und zur technologischen Reife für die Kupfererzeugung gebracht wurde. 1926 wurde die Bessemerei auf der Gottesbelohnungshütte in Betrieb genommen. Bei der Standortwahl war auch bestimmend, dass hier - noch aus den Zeiten des Röstverfahrens - bereits eine Kontaktanlage zur Verwertung der SO2 -haltigen Abgase existierte. Der nun eingeführte Verblaseprozess erfordert flüssigen Rohstein als Input. Wegen der dezentralen Rohsteinerzeugung war jedoch ein Flüssigtransport nicht gegeben.
Also wurde der Rohstein in einem Schachtofen aufgeschmolzen und vor dem Chargieren im Konverter gesammelt. Beim Verblaseprozess wird zuerst das Eisensulfid oxidiert. Das Eisen wird dann durch Quarzzuschlag verschlackt. Übrig bleibt Spurstein, also Kupfersulfid. Das Verblasen dieses Spursteines erfordert große Sorgfalt. Sukzessive bildet sich durch den Verblaseprozess Kupfer. Dazu wird der Konverter so gedreht, dass die Luft in die Spursteinphase kommt (Bild 14).
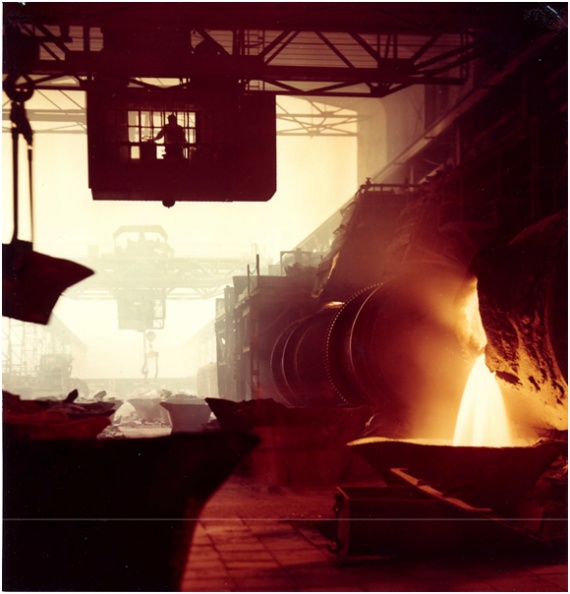
(Foto Archiv Mansfeld Museum, Hettstedt)
Das Eisen des geschmolzenen Rohstein wird in der ersten Verblaseperiode zu einer Fayalitschlacke (2FeO x SiO2) verschlackt, die vor dem Verblasen des Spursteines entfernt werden muss.
Die SO2-haltigen Abgase wurden über eine Rohrleitung in die Kontaktanlage geleitet, wo das SO2 durch V2O5-Katalysatoren zu SO3 oxidiert wurde. Das SO3 wurde ausgewaschen und es entstand Schwefelsäure.
Am Ende des Verblaseprozesses erhält man Schwarzkupfer mit 0,5 bis 0,6 % Silber, etwas weniger Nickel und Blei. Die Weiterverarbeitung dieses Schwarzkupfers veränderte das Gesicht der Gottesbelohnungshütte weiter. Der Betriebsteil Flammofenbetrieb wurde zur Raffination des Schwarzkupfers zu Anodenkupfer weiter entwickelt.
1937 ging die Kupferelektrolyse auf der Gottesbelohnungshütte in Betrieb. Es handelte sich dabei um eine Raffinationselektrolyse. Mit der Anwendung des Elektrolyseverfahrens waren nahezu alle Nachteile der bisherigen Technologien zur Entsilberung von Kupfer beseitigt. Im Elektrolyseverfahren wird das Anodenkupfer durch Einwirkung von Gleichstrom aufgelöst. Mit dem Kupfer löst sich auch das Nickel auf und verbleibt im schwefelsauren Elektrolyten, aus dem es entfernt werden muss – durch Auskristallisation. Silber und weitere Edelmetalle sowie Blei und Selen sammelten sich im Anodenschlamm, der bis zu 50 % Silber und 7 % Selen enthielt und vergleichsweise zur vorherigen Arbeitsweise ein ideales Vorprodukt für die Silber- und Selenherstellung war. An der Katode scheidet sich Kupfer mit 99,95 % Kupfer ab (Bild 15).
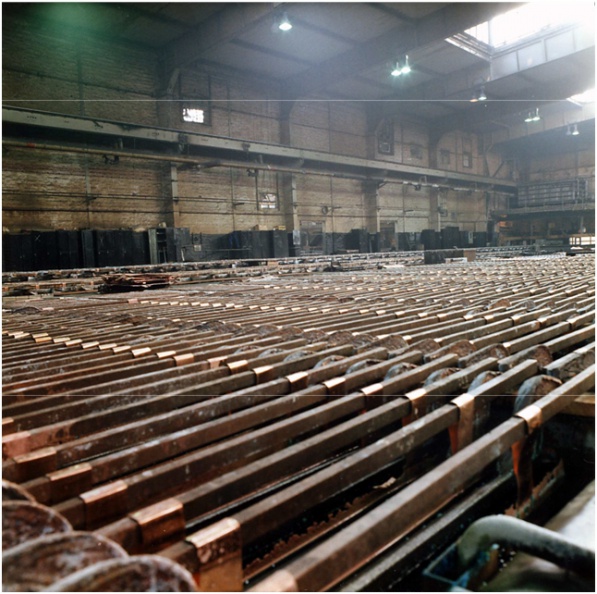
(Foto Archiv Mansfeld Museum, Hettstedt).
Die Katoden wurden als Hauptprodukt der Elektrolyse zunächst im Flammofen zu Formaten verarbeitet.
In den 1960er Jahren wurde die Formateproduktion durch zwei Strangussanlagen erweitert, in denen sauerstofffreies Kupfer hergestellt werden konnte. 1978 erreichte die Katodenverarbeitung in einer Drahtgießwalzanlage ein weiteres technologisches Highlight, verbunden mit tief greifenden Veränderungen bei der Weiterverarbeitung im benachbarten Walzwerk Hettstedt (heute MKM). Die Kapazitäten der Gießanlagen wuchsen stärker als das eigene Aufkommen an Katoden, sodass zunehmend Fremdkatoden zu gekauft werden mussten.
Auch für die Anodenschlammverarbeitung musste eine neue Technologie entwickelt werden. Das Material wurde geröstet, um das Selen in lösliches Selenit zu überführen; das Röstgut anschließend gelaugt. Dieser Prozess wurde ab 1980 durch eine Drucklaugung ersetzt. Das Selen konnte dann mit SO2 ausgefällt und bis zum Reinstselen gereinigt werden. Der Laugerückstand, mit Schwefelsäure entkupfert, lief dem Silberflammofen vor, in dem Anodensilber hergestellt wurde, das wiederum der Silberelektrolyse vorlief. Endprodukte der Silberelektrolyse waren reines Silber und Anodenschlamm, der die restlichen Edelmetalle enthielt und in Fremdbetrieben weiter verarbeitet wurde.
Mit zunehmender Industrialisierung kam immer mehr Sekundärkupfer in Form von Legierungen aber auch in metallischer und verunreinigter Form in größeren Mengen auf den Markt und stand als Rohstoff für die Kupferhütten zur Verfügung. Insbesondere in Krisen- und Kriegszeiten, wenn es zu akutem Metallmangel kommt, werden gern „Altmetalle“ mobilisiert.
So kam es, dass 1942 in Verlängerung der Rohsteinkonverterkranbahn der Bessemerei ein 8. Konverter für das Schrottverblasen nach dem Knudsenprozess in Betrieb genommen wurde. Das Verfahren ist effektiv und unkompliziert. Der Konverter wird mit einem Koksbett aufgeheizt. In das glühende Koksbett wird Messingschrott eingetragen. Das Messing schmilzt und in die flüssige Metallphase wird Luft eingeblasen. Eisen und Zink verbrennen exotherm und liefern die Schmelzwärme für das nachfolgende Material. Zink geht als ZnO in den Flugstaub, Eisen wird verschlackt. Weitere Begleitmetalle wie Blei und Zinn werden auch verflüchtigt. Am Ende des Verblaseprozesses erhält man Schwarzkupfer. Aus den Abgasen wird Pb/Zn/Sn-haltiger Flugstaub gewonnen.
Die Entwicklung der Sekundärmetallurgie war auch zu DDR-Zeiten interessant. So entstand 1969 bis 1972 eine neue Sekundärkupferanlage auf der Kupfer-Silber-Hütte (Gottesbelohnungshütte). Sie verfügte über einen Schachtofen zur Verarbeitung der oxidischen Materialien und der Konverterschlacke sowie über zwei Konvertoren. Die metallurgischen Aggregate verfügten über eine Gasreinigung (Sackfilteranlagen). Das Schwarzkupfer der Sekundärkupferanlage lief dem Anodenbetrieb vor, wodurch das Primärkupfer (aus Erz) verdünnt wurde und somit der Silbergehalt der Anoden abnahm. Die zunehmenden Anteile an Sekundärkupfer bedingten auch Veränderungen in der Prozessführung der Elektrolyse. Damit ist der Kupferweg, den die Mansfelder Metallurgen beschritten haben, bis in die Neuzeit beschrieben und soll in der nachfolgenden schematischen Darstellung vereinfacht gezeigt werden (Bild 16).
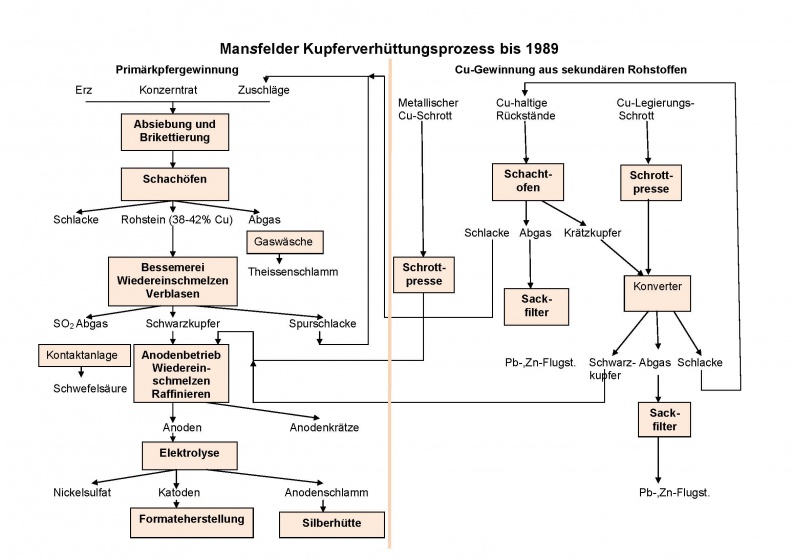
1998 kam zwar noch ein neuer Anodenbetrieb hinzu, doch der Schrottmarkt wurde komplizierter und die Konkurrenzhütten hatten durch moderne Schmelzverfahren mit hoher Kapazität aufgerüstet. 2002 erfolgte die Stilllegung der Anlagen, was mit dem Ende der Metallgewinnung gleich zu setzen ist.
Eine Beschreibung, die sich auf den Hauptprozess, also die Kupfergewinnung beschränkt, würde das Mansfelder Hüttenwesen mit seinen weltweit einmaligen - rohstoffbedingten - Prozessen nicht ausreichend repräsentieren. Unverzichtbar ist und bleibt in diesem Zusammenhang die Erwähnung der anspruchsvollen Technologie der Theissenschlammverarbeitung (Zn-Pb- und spurenmetallhaltiger Flugstaub der Rohhütten). Für die Theissenschlammverarbeitung wurde die Kupferkammerhütte zur Bleihütte umgebaut. Der Prozess der Verarbeitung ist allerdings erst allmählich gewachsen. Der Theissenschlamm musste zunächst vom Bitumen befreit werden. Das erfolgte auf den Rohhütten bzw. nach Stilllegung der Krughütte (Karl-Liebknecht-Hütte) im Jahre 1972 allein auf der Kochhütte (August-Bebel-Hütte) durch Schwelen.
Man begann, den Theissenschlamm im Schachtofen zu verarbeiten. Das erwies sich als unbefriedigend und in der Folgezeit wurde die Bleihüttentechnologie immer wieder verändert und angepasst. Den Verarbeitungsversuchen im Schachtofen zur Schwelgutverarbeitung folgte der Einsatz von Kurztrommelöfen, in denen Zinkklinker und Bleioxid hergestellt wurden, die dann in technologisch anspruchsvollen Schritten weiter verarbeitet wurden. Die laufend notwendigen Veränderungen waren auch der Tatsache geschuldet, dass sich die Zusammensetzung des Schwelgutes zuungunsten des Bleis veränderte. Durch intensive Forschungsarbeiten gelang es, das differenzierte Wälzen zu entwickeln. Dabei wurde im ersten Wälzofen das Blei vom Zink getrennt, wobei das Blei in den Flugstaub ging.
Der Flugstaub wurde zur Extraktion von Re und Cd mit heißem Wasser gelaugt. Der Laugerückstand gelangte in eine Klinkertrommel zur Herstellung eines Bleiklinkers. Blei wurde dann im Schachtofen erschmolzen. Zink ging in den Zinkklinker, der entweder aufgehaldet oder einem 2. Wälzofen zugeführt wurde, um das Zink zu verflüchtigen. Aus dem Zinkoxid wurden Farbzinkoxid und Zinksulfat hergestellt. Das differenzielle Wälzen galt als hüttenmännische Meisterleistung, blieb aber auch keine Lösung für immer.
Zum Schluss verzichtete man auf das differenzielle Wälzen und stellte in einem Wälzofen ein Pb-Zn Mischoxid her aus dem durch Laugung Zinksulfat gewonnen wurde. Den Blei-Rückstand dieser Verarbeitung schmolz man im Schachtofen zu Werkblei um und verkaufte dieses zur Weiterverarbeitung an die Bleihütte Freiberg, nachdem die eigene Bleiraffination aufgegeben wurde. Große Bedeutung besaß die Bleihütte als Produzent von Spurenmetallen aus den Stäuben, die bei der Verhüttung anfielen. So wurde aus verschiedenen Anreicherungsprodukten, die im technologischen Prozess der Bleihütte anfielen, ein Zwischenprodukt mit 40%igem Cadmium sowie Rhenium, Thallium, Jod und Germanium hergestellt und in den Handel gebracht.
Nachfolgend (Bild 17) ist der Bleihüttenprozess aus der Zeit Anf. der 60er Jahre in einer stark vereinfachten Grafik dargestellt. Kein anderer Prozess war so vielen Veränderungen ausgesetzt. Das erfordert eine Beschränkung und starke Vereinfachung. Wenn man den Bleihüttenprozess in allen Varianten und Nuancen verstanden hat, konnte man „Metallhüttenkunde“ wirklich.
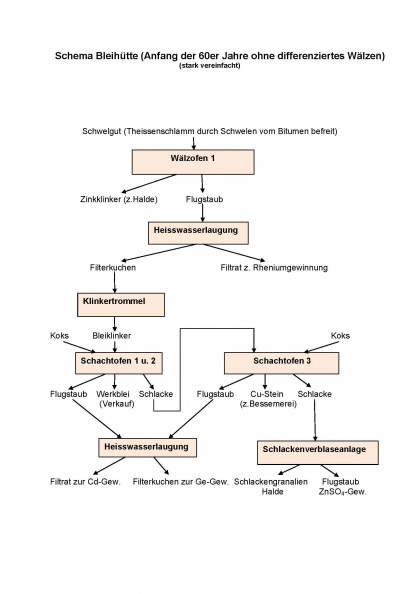
Die Bleihütte wurde mit der vollständigen Inbetriebnahme der Sekundärkupferanlage Anfang der 70er Jahre geschlossen. Seitdem wurde der weiter auf der Rohhütte anfallende Theissenschlamm deponiert.
Spätestens ab diesem Zeitpunkt zeichnete sich langfristig ab, dass der Bergbau auf Kupfer im Mansfeldischen endlich sein wird. Eine Herausforderung - auch für den Hüttenmann - stellte die damals beabsichtigte Erschließung der Lagerstätte Spremberg dar. Sie führte zu umfangreichen Untersuchungen zur Verarbeitung von Spremberger Konzentrat. Eine neue Kupferhütte wurde entworfen. Heute wissen wir, dass die Kraft der DDR für das Projekt Spremberg nicht reichte.
Dieser Beitrag wäre unvollständig, wenn man nicht auf eine der schönsten und instruktivsten Prozessbeschreibungen eingehen würde: Den Mansfeld-Stammbaum. Nichts bringt den Mansfeld-Prozess besser und auch schöner auf ein Blatt Papier (Bild18). Für mich ist das nicht nur eine technische Darstellung, sondern ein echtes Kunstwerk und ganz früher war Metallhüttenkunde eine Kunst, der man ruhig einmal mit dieser Darstellung huldigen kann. Sie zeigt auch die enorme Vielfalt der Ergebnisse vor Forschung und Innovation des 20. Jahrhunderts. Nun: Es ist heute Geschichte.
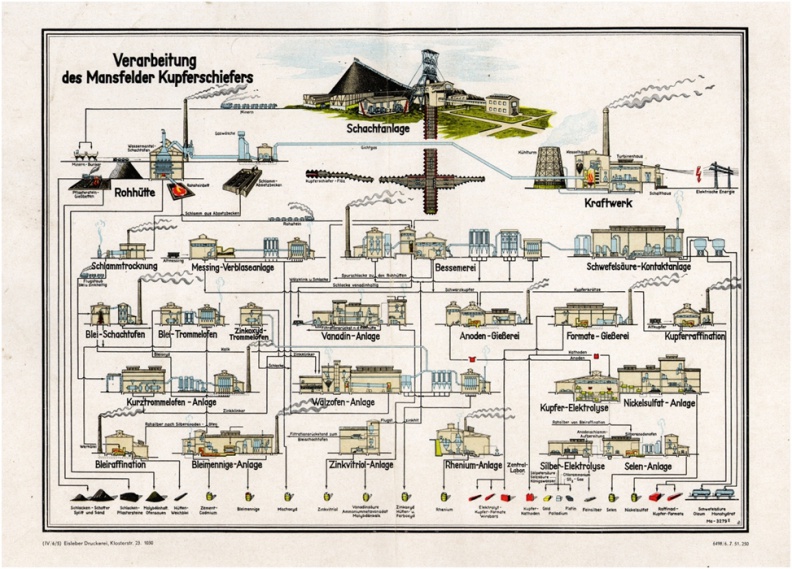
5. Schlussbetrachtung
Auch nach Auslaufen des Mansfelder Bergbaus gab es immer wieder Überlegungen zur Nutzung von Haldenmaterial als potenzieller Rohstoff neuer Verarbeitungsprozesse zur Gewinnung der wertvollen Inhaltsstoffe. Wir wissen, dass das Mansfeldkupfer seit 1931 wegen der hohen Kosten bei seiner Herstellung subventioniert worden ist, das ging so bis in die jüngere Vergangenheit. Wenn man also Überlegungen anstellt, die Mansfelder Metallurgie wiederzubeleben, sollte man vor Beginn von Forschungsarbeiten einen Stift und ein Blatt Papier in die Hand zu nehmen und rechnen: Wie viel Metall ist im Material, wie groß sind die wirtschaftlich verfügbaren Vorräte und wie viel kann man somit letztlich erlösen. Dann rechne man überschlägig die Kosten für Transport, Aufbereitung, und Reststoffentsorgung und ganz überschläglich auch für Verhüttung (gegebenenfalls mit Investkosten für die Erstellung der Technik bis hin zu deren Entsorgung nach Aufbrauchen der Rohstoffvorräte) oder die hüttenmännische Lohnarbeit bei Verkauf an Dritte ein. Wenn man das seriös macht, wird man schnell den Stift beiseitelegen. Wenn sich die Welt nicht ganz unvorhersehbar und auch schwer vorstellbar verändert, sollten wir sagen: Die Mansfelder Berg- und Hüttenleute hatten knapp 800 erfolgreiche Jahre und sie sollten sich im Nachgang daran erfreuen. Es gehört nicht zu ihrer Tradition und ihrem Wesen, sich mit völlig unrealistischen Dingen zu beschäftigen.
(Stand 01/2019)